Fat finger problem
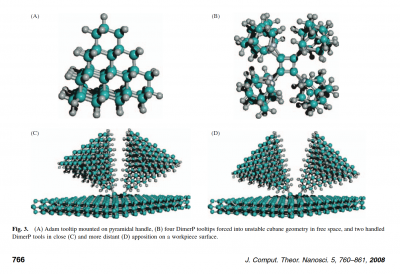
Because the "fingers" of a manipulator mechanism (not "arms" those lack stiffness) must themselves be made out of atoms, they have a certain irreducible size. Thus one might worry that there just isn't enough room in the nanometer-size reaction region to accommodate the number of "fingers" necessary for performing the desired atom by atom reactions.
As it turned out:
- Most reactions in diamondoid mechanosynthesis can be performed with three or less tip shaped "fingers" (see "sticky fingers" page).
- A halve space (2π steradian) e.g. above a flat work-piece can accommodate four sufficiently stiff "fingers" leaving each "finger" still enough room to tilt and move (full space consequently can accommodate twice as much that is eight fingers).
(wiki-TODO: find and link the discussion & pictures of this)
Contents
"Fingers fatness" in earlier productive nanosystems
In technology level I there is only the need to put together previously selfassembled building blocks. Due to the size of the preselfassembled blocks the size constraints on the "fingers" aren't very critical in these early systems. VdW force hydrogen bonds & co should suffice for holding the pieces so there is no essential need especially fat "fingers" that operate like pincer grip pliers. (This crosses over to Stickly fingers).
In technology level II (a level which might be skipped) the manipulating "fingers" for early mechanosynthesis may look more like bio-mineralization enzymes and thus may be a bit bulky limiting capabilities.
By designing foldamers (proteins or others) with de-novo methodology and adding stiffer molecules (like e.g. spiroligomers),
it might be possible to make proper stiff independently changeable "fingers" much more compact and pointy in than natural examples (biomineralization).
As of 2017 still very little work has been done in this area.
(TODO: Research in "in solution piezochemical mechanosynthesis" is urgently needed.)
(Biomineralization enzymes aren't big specialized enzymes for mediating complex reactions between very specific big floppy molecules so they most of their volume is made up by interface structure which can potentially be shrunk for integration in an artificial system.)
Possible origins of fat finger concern
On the first few pages of the book "Engines of Creation" (page 13 & 14) a programmable protein machine is described in brevity. This machines is described to grasp both a large rounded lumpy molecule (the workpiece) and a small molecule, then bringing the small one up against the big one in a specific location. This adds the small molecule to the workpiece. Instead of building loosely folded (chain polymer based) proteins this artificial programmable protein machine would build small solid rugged objects. Three examples for materials for these objects are given: metals, ceramics (aka gemstones) and diamond.
Knowledgeable readers will be aware of the issues with the mentioned materials:
- synthesis of diamond (and some ceramics) involves chemically highly reactive intermediate steps
- synthesis of (non-noble) metals has the concern of undesired oxidization undesired surface diffusion
Due to these issues one needs to conclude that the programmable protein machine would need to perfectly tight-seal-pan-cake-like-form-fit whatever the workpiece looks like at the moment to keep unwanted stuff out preventing it from messing up the reaction site.
Since the shape of the workpiece may change a lot during buildup this tight-seal-pan-cake-like-form-fit might seems rather impossible since proteins (while being flexible) do not behave like rubber gaskets (not to speak of pushing every last molecule out). Either the hypothetical "fat finger"-enzyme is leaky or the "fat finger" is in the way. Thus this might a source for the "fat finger" critique.
But this was a very early version of the incremental path (incremental path = using self assembled systems to get to full positional control ASAP) that was still very crude and still too direct, jumping from (almost) natural protein systems right away all the way to the most advanced target material: diamond.
By now the details about the incremental path have become somewhat clearer though.
A more detailed multi step bootstrapping process is presented in the appendix of the newer book "Radical Abundance".
In short:
The "tight-seal-pan-cake-like-form-fit" problem can be avoided entirely by taking a small detour over ceramic (aka gemstone) materials that are synthesizeable in a solution phase environment.
Misc
The irreducible size of "fingers" has some other nontrivial consequences too.
The lower spacial production density compared to solution phase chemistry must be compensated via:
- higher speed (~MHz range -- but not to high to avoid excessive friction -- not ~GHz range)
- higher reaction success rate (comes naturally)
- more compact (hard-coded mill style) designs instead of the now obsolete molecular assemblers
- stacking of the bottom-most assembly levels
Going doen the assembly levels: While the assembly cells quickly get smaller the whole stacks of them get bigger (at the bottommost layers). One can find that this is shown in the "Productive Nanosystems" concept video, if one watches attentively.
See main page: Achieving sufficient effective atom placement frequency
Notes
- (wiki-TODO: There was a web-page illustrating that up to four stiff diamondoid tips fit above a flat surface simultaneously acessing the same atom. Find and add the link. (vanished)? -- Also make a sketch of that and add as main illustrating image to the page.)
Related
- Sticky finger problem
- (Sloppy finger problem)
- Up: The finger problems
- Learning from enzymes
- Mechanosynthesis
- Separation of concerns
- History