Intercrystolecular snapping modes
What is considered a to be a "snap" here?
A more or less forced slow motion (nm/s to mm/s) causing
– a sudden removal of motion constraints and following
– a more or less violent fast mechanical relaxation near the speed of sound (many m/s to km/s)
The forced motion can but does not need to provide the majority for the energy for the snap
it can also just release energy that has been stored in the system at an earlier time.
The forced motion must merely provide enough energy to overcome the activation energy for the snap.
To give some more additional intuition on the intended meaning of "snaps" here
there is a section "electrical analogy to mechanical snaps" at the end.
(wiki-TODO: add illustrative images)
Contents
[hide]- 1 Slide (freely to max contact area) snapping
- 2 Notch snapping
- 3 Clap snapping
- 4 Bend snapping – and other snapping modes
- 5 Entropic snaps
- 6 Electrical analogy to mechanical snaps
- 7 Why to avoid snaps (locally and nearby remotely)
- 8 When to tolerate snaps
- 9 When to seek snaps
- 10 Relation of snaps to maximally possible assembly speed
- 11 Related
Slide (freely to max contact area) snapping
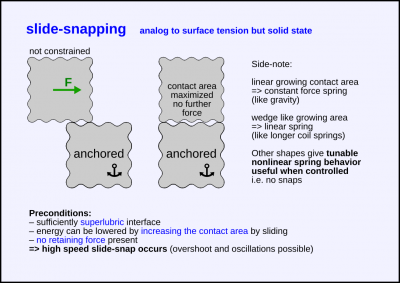
A crystolecule is released while suberlubrically contacting an other crystolecule.
The crystolecule will snap to the location and orientation of maximal surface contact area (surface tension analogy).
Perhaps the most obscure / unexpected one of the snapping modes.
This snapping mode is related to the wedge slide force that should be very useful
for the creation of compact and tunable (constant/linear/nonlinear) weak force springs.
Related: VdW suck-in
Level of energy
- quite weak, less than bend snapping
- likely less than notch snapping in most if not all cases (for same surface area)
=> thus the need for superlubric interfaces for this snapping mode to be available
Notch snapping
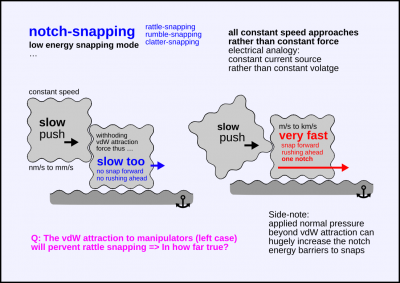
A crystolecule part contacts an other one and snaps to the next notch in commensurate atomic alignment.
I.e. the atomic patterns interdigitate and there's a jump to the next notch due to a shearing force.
Notch snapping can likely be avoidable in assembly and disassembly of structures,
It seems likely that in most cases such snaps are prevented by larger back-holding forces.
In particular face-to-face sticking vdW forces towards the actuating part may prevent notch snapping.
It depends on the ratio of surface areas.
It may even be slightly challenging to intentionally provoke a notch snap.
Cases of weaker back-holding forces that notch snapping forces may be able to overcome:
– shifting a part with merely an edge or a corner of an other part (low attractive vdW forces)
– competition with higher energy notch snapping on a second contacting surfaces that is forcibly moved
– Superbubic sliding to maximize contact area (surface tension analogy)
Level of energy
- low energy snapping mode
Clap snapping
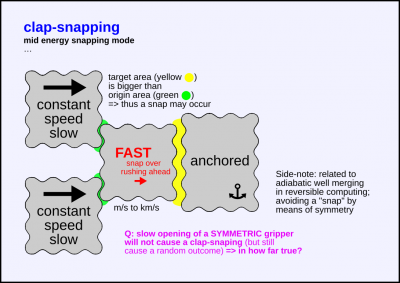
A crystolecule part snaps over from a smaller contact area to a bigger contact area.
Flat on flat like a clap thus the choice of name.
In symmetric cases like with parallel acting gripper claws,
there won't be a snap so long the holding forces before the gripping
exceed uncompensated forces form imperfections in the symmetry of the approach of the gripper.
Side notes:
– Grippers might for the most part not be necessary due to exploitability of vdW sticking forces.
– During symmetric gripper opening without a definite target (in free space or on superlubric surface),
there will be no snap but a one bit of entropy truly random outcome on which side of the gripper the part will end up.
See related page: Well merging and splitting
Level of energy
- mid energy snapping mode
- can possibly be > covalent bond energy given enough area acting
Bend snapping – and other snapping modes
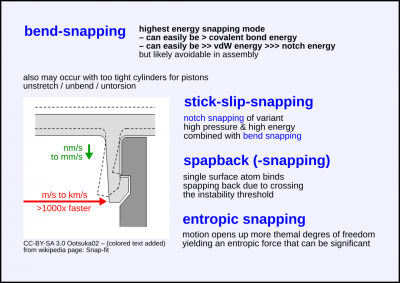
A crystolecule part is bent and then suddenly released without any back-holding force.
Many covalent bonds are stretched and they can be stretched/strained to a high degree.
More than 10% (see page: Superelasticity).
Thus such snaps can release a huge amount of energy.
Bend snapping can likely be avoidable in assembly and disassembly of structures,
it may sometimes be desired, but in most cases weaker energy barriers should easily suffice
i.e. easily prevent thermally activated fall-apart even for the highest expectable temperatures.
Level of energy
- high energy snapping mode
- can easily be > covalent bond energy
- can easily be >> vdW energy >>> notch energy
(all meant per unit area)
Stick-slip-snapping
A combination of high pressure notch-snapping and bend-snapping.
Level of energy perhaps somewhere in-between?
Surface atom bond snapback
See main page: Snapback
This is sort of surface localized bend snapping.
It can be just single individual covalent bonds that snap back from a bent position
This snapping is not to confuse with notch-snapping which is similar yet quite different.
(wiki-TODO: Elaborate on that.)
Level of energy
- depends on the number of bonds bent
- much less than bend snapping as it is located on surface only
- much more than notch snapping as the benting of covalent forces is involved, not just redirected vdW forces
Entropic snaps
Snaps caused by entropic forces.
I.e. motions unlocking thrmal degrees of freedom.
This may be significant!
See also related page: Accidental heatpump
Level of energy
(TODO: Level of energy of entropic snaps remains to be determined.)
Electrical analogy to mechanical snaps
To give some additional intuition on the intended meaning of "snaps" here:
In the mechanical-electrical analogies a snap would roughly correspond to the following scenario:
– there is a capacitor as source (representing the initial system energy)
– there is quickly switching capable (FET) transitor (representing the sudden removal of mechanical constraints against motion)
– the leads to the load are short circuited (representing the near absence of loads once the snap has started)
Quickly opening a switching transistor while the leads to the load have been short circuited gives – a very high current (analog to very fast motion) – possibly some overswinging and very high frequency oscillations due to the minute inductivity of the circuits single loop (as in "silde snapping" below) – quite quick loss of the total systems energy into heat
Why to avoid snaps (locally and nearby remotely)
- Misplacements during assembly of nano- and microscale parts
- Disturbance of mechanosynthesis (the same energy in non-thermal spectrum can have much higher amplitudes)
- Energy dissipation: Coolability and energy efficiency. Relevant for advanced systems.
The fewer the snaps the higher the assembly speed and throughput can be so long dissipation from snaps is the bottlenecking factor. Especially likely at large nanoscale microscale and lower mesoscale.
The cost to avoid snaps lies in some additional system complexity and in system remaining overhead.
When to tolerate snaps
Basically the inverted list: In case snaps …
- … do not disturb mechanosynthesis too much
- … do not lead to unacceptable misplacement rates in nano- and microscale parts
- … are not the dominant energy dissipation mechanism
Plus in case of cost of snap-avoidance is too high. In case allowing snaps …
- … hugely simplifies the system design (complexity)
- … reduces permanent in-system-remaining overhead (size, volume, mass).
E.g. no needs of the complexities imposed by energy recuperation.
When to seek snaps
Active dissipation machine elements.
Possibly better many weak snaps
rather than few huge ones
to avoid huge mechanical shocks.
In mechanical electrical analogy: Better shorting small capacitors often than one huge one once. This better approimates an electrical resistor as useful circuit element.
(wiki-TODO: Perhaps further elaborate on that.)
Relation of snaps to maximally possible assembly speed
For ultra high speed pre-mechanosynthesized part recomposing in on chip microcomponent recomposers or related devices
system architectures (structural element making frame systems, housings, and more; and various machine elements)
may want to refrain from using any but the bare minimum of lowest energy snaps in the (dis)assembly process.
Note that not all clips mean snaps.
One can energetically reversibly actuate clips.
To still prevent the whole system from running backwards (i.e. to get an arrow of time)
One could perhaps employ the (on this wiki first introduced) trick of exothermy offloading.
This would allow for no snaps at all in the assembly zone with
the necessary minimal dissipation to drive the system forward (could also be seen a snaps)
all shifted over to the drive zone where this can be better controlled and optimized.
The concern here is that coolability may become the bottleneck to speed.
But other loss mechanisms may become dominant making further optimization on minimizing losses from snaps pointless. E.g.:
- Losses from sliding friction as it starts growing rapidly with higher speeds (~square law). See page: Friction & Friction in gem-gum technology.
- Losses form inefficiencies in high energy turnover non-snappingly more reversibly actuated clips.
- Losses from exothermy offloading energy transport between the zones.
To the last point: Yes, clips can be actuated without snaps by doing energy recuperation.
Again: Clips do not necessarily mean snaps!
Energy recuperation is also a case with energy transport back to the drive zone.
Related
- Intercrystolecular interactions
- Intercrystolecular snapping modes < you are here
- Intercrystolecular levitation
- Assembly from atomically precise nanoscale and microscale parts
- Assembly level 2 (gem-gum factory) & Crystolecule assembly robotics & Sequence of zones
- Lagrangian mechanics for nanomechanical circuits – for how violent sharp shocks propagate to the system
- Mechanical-electrical analogies – constant speed sources (in analogy to constant current sources) prevent can prevent undesired snapping
- VdW suck-in – slide snapping
- Accidental heatpump – entropic snap (?)