Difference between revisions of "Design of gem-gum on-chip factories"
m (→Convergent assembly) |
m (→Related: fixed link) |
||
(53 intermediate revisions by the same user not shown) | |||
Line 1: | Line 1: | ||
− | + | For a general overview over advanced atomically manufacturing the [[technology level III|technology level III page]]. | |
− | [[ | + | For a less technical overview about nanofactories check out the [[nanofactory|general overview page]]. |
* (folding) | * (folding) | ||
Line 7: | Line 7: | ||
* [[Design levels]] | * [[Design levels]] | ||
* [[Control levels]] | * [[Control levels]] | ||
+ | |||
+ | Links to relevant quantitative details here can be found here: | ||
+ | * [[Gem-gum factory design parameters]] | ||
+ | * [[Nanofactory math based on continuity of throughput]] | ||
+ | * [[Pages with math]] | ||
+ | |||
+ | = Basic energy balance = | ||
+ | |||
+ | As carbon carrying resource material the fuel gas '''methane (CH<sub>4</sub>)''' or the welding gas '''acetylene (C<sub>2</sub>H<sub>2</sub>)''' is used. | ||
+ | When those gasses are not burned but are being put together to products there still remains '''a lot of excess energy'''. | ||
+ | |||
+ | * '''heating values:''' CH4 55,5MJ/kg > C2H2 49,9MJ/kg '''>''' Cn 32,8MJ/kg (graphite) | ||
+ | |||
+ | As resource material the carbon carrying "exhaust-gas" '''carbon dioxide (CO<sub>2</sub>)''' in ambient air can be used too. Its like "ash" on the lowest end of the carbon combustion chain thus the heating value of zero. If it is used as building material '''high amounts of energy are needed'''. | ||
+ | |||
+ | * '''heating values:''' CO2 0,0MJ/kg '''<''' Cn 32,8MJ/kg (graphite) | ||
+ | |||
+ | == Personal fabricator as stationary device == | ||
+ | |||
+ | Depending on the used building material the needed or excessive energy must be taken from of fed into the power grid. <br> | ||
+ | Gas lines (CH<sub>4</sub>) and atmospheric CO<sub>2</sub> lend themselves as existing building material supply. | ||
+ | |||
+ | Related: [[Form factors of gem-gum factories]] | ||
+ | |||
+ | == Personal fabricator as portable device == | ||
+ | |||
+ | Huge amounts of energy cannot be provided from the small device. | ||
+ | The resource-gasses (e.g. CH<sub>4</sub> or C<sub>2</sub>H<sub>2</sub> in capsules) must thus carry along enough energy for production. | ||
+ | Simply radiating excessive heat away may slow down production significantly because of the high chemical energies involved. | ||
+ | It may be better to balance the excess energy roughly to zero by using atmospheric CO<sub>2</sub> as building material too. | ||
+ | To pump high volumes of air silent [[Medium movers|medium mover]] metamaterials can be used. | ||
= Convergent assembly = | = Convergent assembly = | ||
− | + | See main page: [[Convergent assembly]] | |
− | * | + | |
− | * | + | * Convergent assembly should not be confused with with exponential assembly which is an [[exponential assembly|entirely different concept]]. |
+ | * Convergent assembly (putting things together in a hierarchical way) is not a means to speed up production in general. | ||
+ | * The motivations for why to do convergent assembly are outlined on the its main page. | ||
* The lowermost three convergent assembly steps follow naturally from the character of the technology - see [[assembly levels]] to understand this. | * The lowermost three convergent assembly steps follow naturally from the character of the technology - see [[assembly levels]] to understand this. | ||
+ | |||
+ | Covergent assembly crossing so many sizescales poses a challenge to visualizing it and making it intuitively comprehensible. | ||
+ | Possible ways to visualize convergent assembly include: | ||
+ | * [[Distorted visualisation methods for convergent assembly]] – all in one picture | ||
+ | * Animating a fly-through with continuous scaling | ||
= Nanosystem units = | = Nanosystem units = | ||
== [[Robotic manipulators]] == | == [[Robotic manipulators]] == | ||
+ | |||
+ | * Nanoscale: [[Molecular mills|mill style robotics]] | ||
+ | * Microscale: [[parallel robotics]] – delta-bots, steward-plattforms, parallel scaras, patallel gantry bots | ||
+ | * Microscale to mesoscale: [[part streaming robotics]] | ||
+ | * Mesoscale: [[serial robotics]] – classical scara bots, classsical robot arms | ||
+ | * Macrocscale: [[dexterous tentacle style robotics]] (part streaming) | ||
== Threading by systems == | == Threading by systems == | ||
+ | |||
+ | Main page: [[Subsystems of gem-gum factories]] | ||
+ | |||
+ | * [[Assembly subsystem]] – Related: [[Routing levels]] | ||
+ | * [[Vacuum subsystem]] | ||
+ | * [[Coumputation subsystem]] | ||
+ | * [[Energy subsystem]] | ||
+ | * [[Thermal subsystem]] – Related: [[Thermal management in gem-gum factories]] | ||
== Cooling, vacuum and other logistics == | == Cooling, vacuum and other logistics == | ||
Line 25: | Line 77: | ||
* [[Vacuum handling]] | * [[Vacuum handling]] | ||
* [[Thermal isolation]] & [[Diamondoid heat pump system]] | * [[Thermal isolation]] & [[Diamondoid heat pump system]] | ||
+ | * [[Medium mover]]s for air supply | ||
= Macroscopically separating design considerations = | = Macroscopically separating design considerations = | ||
− | + | The first two processing steps are: | |
+ | * capturing resource molecules from liquid phase and purifying them by sorting mills and | ||
+ | * mechanosynthetic [[tooltip preparation]]. | ||
− | + | It makes sense to do the former in a warm environment and the latter in a cold environment. <br> | |
− | Although | + | In order to avoiding freezing of solvent and minimize error rates respectively.<br> |
− | it seems rather easy to do (see: "[[Diamondoid heat pump system]]") and error rates can be shrunken by many orders of magnitude. | + | Macorscopic separation (possibly even in physically separate devices connected by a [[matter conducting wire]]) could be considered. |
+ | |||
+ | '''Cooling and isolation:''' <br> | ||
+ | Although [[piezochemical mechanosynthesis]] works at room temperature cryogenic cooling will probably be employed just because | ||
+ | * it seems rather easy to do (see: "[[Diamondoid heat pump system]]") and | ||
+ | * error rates can be shrunken by many orders of magnitude. | ||
= General nanofactory design method = | = General nanofactory design method = | ||
− | Given a set of "base units" for different components of the | + | Given a set of "base units" for different components of the bottom-most assembly levels <br> |
+ | their combination to form a full nanofactory unit can be determined by <br> | ||
+ | first finding the relevant quantitatively or at least qualitatively (set of choices) of evaluable relevant metrics and <br> | ||
+ | determine numbers of base units and branching factors based thereof. <br> | ||
+ | ([http://en.wikipedia.org/wiki/Constraint_logic_programming constraint logic programming] - [http://www.swi-prolog.org/man/clpqr.html prolog library clpqr]?) might be useful. | ||
+ | |||
+ | * '''condition to be fulfilled:''' output frequency of an assembly level == input frequency of the assembly level directly above – See: '''[[level throughput balancing]]''' | ||
+ | |||
+ | {{Wikitodo|This section needs reformulation!}} | ||
= Design metrics = | = Design metrics = | ||
+ | |||
+ | * ratio of manipulator to building block in volume, number of atoms or mass | ||
== Performance limits == | == Performance limits == | ||
Line 44: | Line 114: | ||
The ultimate performance limit is determined by the accepted dissipation heat at the lower levels the maximal acceptable accelerations at the higher convergent assembly levels. Designs leading to practical speeds at human scale lie way below the performance limits. | The ultimate performance limit is determined by the accepted dissipation heat at the lower levels the maximal acceptable accelerations at the higher convergent assembly levels. Designs leading to practical speeds at human scale lie way below the performance limits. | ||
− | + | Power dissipation is only a limiting factor at the bottom-most assembly levels. At higher assembly stages bearing area per volume drastically falls. | |
+ | If bearing volume is kept constant [[infinitesimal bearings|via stacking]] the total speeds can be dramatically increased till resonance or acceleration limits are hit. Either one accepts overpowered upper layers of the nanofactory which only can be used to their full potential when prefabricated parts are recomposed or one may deviates from the layer structure to a more complicated fractal structure for the bottom layers. | ||
+ | (dynamic drag and breaking losses) | ||
== Threading by pre-products == | == Threading by pre-products == | ||
Line 55: | Line 127: | ||
[[file:Nanofactory - bottom layer slowdown 640x554.png|thumb|400px|Low density of actual mechanosynthesis locations are the reason why the bottom layers in a nanofactory need to be stacked up. [http://apm.bplaced.net/w/images/d/d9/Nanofactory_-_bottom_layer_slowdown.svg SVG] ]] | [[file:Nanofactory - bottom layer slowdown 640x554.png|thumb|400px|Low density of actual mechanosynthesis locations are the reason why the bottom layers in a nanofactory need to be stacked up. [http://apm.bplaced.net/w/images/d/d9/Nanofactory_-_bottom_layer_slowdown.svg SVG] ]] | ||
− | slow speed of [[assembly levels|assembly level 0]]: The mechanisms to assemble parts normally can potentially be smaller than the parts being assembled. Since The mechanisms to assemble minimal sized DMEs need themselves to be DMEs the mechanisms must have a similar size as the products they assemble. Since only a | + | slow speed of [[assembly levels|assembly level 0]]: The mechanisms to assemble parts normally can potentially be smaller than the parts being assembled. Since The mechanisms to assemble minimal sized DMEs need themselves to be DMEs the mechanisms must have a similar size as the products they assemble. Since only a few atoms are added per assembly step the density of actual building sites of atomic size is rather low and consequently mechanisms at the bottommost layers are quite a bit slower than the ones above and need to be included in greater numbers. |
If assembly units of an assembly level produce (pre-)products slower than the size-characteristic frequency the next higher assembly level demands one can stack assembly units and thread by finished (pre-)products. Assembly units can be stacked as long as the size characteristic frequency of the threading by mechanics is not exceeded. | If assembly units of an assembly level produce (pre-)products slower than the size-characteristic frequency the next higher assembly level demands one can stack assembly units and thread by finished (pre-)products. Assembly units can be stacked as long as the size characteristic frequency of the threading by mechanics is not exceeded. | ||
+ | |||
+ | Speed is also limited by the requirement to keep the rate of friction heat generation in bounds. See: [[Scaling laws#Speedup]]. | ||
== Ratios between levels == | == Ratios between levels == | ||
Layer and stage ratios: In any convergent assembly step a step size can be chosen. Big steps limit the maximum possible speed of the considered assembly level step but makes planning and programming more flexible and easier. | Layer and stage ratios: In any convergent assembly step a step size can be chosen. Big steps limit the maximum possible speed of the considered assembly level step but makes planning and programming more flexible and easier. | ||
+ | |||
+ | A step size that is easy on the human mind is 32 since two such steps roughtly span three (dezimal) orders of magnitude (a factor of 1000). | ||
+ | Starting from 32nm only three steps lead to around one millimeter sized products. | ||
+ | |||
+ | === Conservative estimation === | ||
+ | |||
+ | There is reason to believe that steps of this magnitude won't make a nanofactory design unpractical. | ||
+ | Todays homebuilt 3D printers can fill about 20000 voxels in one minute assuming 100 mm/second head movement and 0.3mm lateral voxel size. | ||
+ | (20000 voxels are about the same as 32^3=32768) | ||
+ | Since frequencies scale up with shrinking size going down doesn't change the troughput capacity. | ||
+ | |||
+ | Step sizes will probably just limit high recycling throughput | ||
+ | but not throughput when mechanosynthesis is involved in production. | ||
== Influences of the branching factor == | == Influences of the branching factor == | ||
Line 69: | Line 156: | ||
== Influences of assembly style == | == Influences of assembly style == | ||
− | In any convergent assembly step one can choose from the different [[robotic manipulators]] to do the assembly. Mill style can (with the exception of the bottommost asselmbly level) have the smaller size and higher characteristic operation frequency of the lower assembly level. Single manipulator style assembly have the bigger size and smaller characteristic frequency of the upper assembly level. (Intermediate forms are possible). The choice depends on whether programmability or speed is | + | In any [[convergent assembly]] step one can choose from the different [[robotic manipulators]] to do the assembly. Mill style can (with the exception of the bottommost asselmbly level) have the smaller size and higher characteristic operation frequency of the lower assembly level. Single manipulator style assembly have the bigger size and smaller characteristic frequency of the upper assembly level. (Intermediate forms are possible). The choice depends on whether programmability or speed is the primary concern. |
== More complicated geometries == | == More complicated geometries == | ||
Line 75: | Line 162: | ||
non stratified 3D fractal designs need higher convergent assembly stages (assembly level IV) to hold the structure together. They have the highest possible performance (way above practically needed levels) other limits are likely to kick in at some point. Finding a general design methodology seems to be a hard problem.For physical changes of such a design a complete microcomponent disassembly end reassembly is likely necessary. | non stratified 3D fractal designs need higher convergent assembly stages (assembly level IV) to hold the structure together. They have the highest possible performance (way above practically needed levels) other limits are likely to kick in at some point. Finding a general design methodology seems to be a hard problem.For physical changes of such a design a complete microcomponent disassembly end reassembly is likely necessary. | ||
− | == External links | + | = Notes = |
+ | |||
+ | * {{todo|list basic nanofactory subsystems as exhaustively as possible}}<br> Maybe add these block diagrams: [http://sci-nanotech.com/index.php?thread/15-nanofactory-block-diagram/] | ||
+ | |||
+ | = Related = | ||
+ | |||
+ | * [[Productive Nanosystems From molecules to superproducts]] – only depicts the assembly subsystem | ||
+ | * [[Nanofactory]] more general introduction | ||
+ | * [[Technology level III]] | ||
+ | ----- | ||
+ | * '''[[Subsystems of gem-gum factories]]''' | ||
+ | * [[Thermal management in gem-gum factories]] | ||
+ | * [[Bottom scale assembly lines in gem-gum factories]] | ||
+ | * '''[[Tracing trajectories of component in machine phase]]''' | ||
+ | ---- | ||
+ | * [[Structural elements for nanofactories]] | ||
+ | ---- | ||
+ | * [[Gem-gum factory design parameters]] | ||
+ | * [[Nanofactory math based on continuity of throughput]] | ||
+ | * [[Pages with math]] | ||
+ | |||
+ | = External links= | ||
Articles from E. Drexlers Blog: | Articles from E. Drexlers Blog: | ||
* [http://e-drexler.com/p/04/04/0512molManSystems.html Complete molecular manufacturing systems will have many subsystems, designed to meet many constraints] | * [http://e-drexler.com/p/04/04/0512molManSystems.html Complete molecular manufacturing systems will have many subsystems, designed to meet many constraints] | ||
* [http://e-drexler.com/p/04/04/0505prodScaling.html Physical scaling laws enable small machines to be highly productive] | * [http://e-drexler.com/p/04/04/0505prodScaling.html Physical scaling laws enable small machines to be highly productive] | ||
+ | * [http://www.imm.org/reports/rep041/ Josh Hall about scaling laws in productive nanosystems] | ||
− | + | = External references= | |
* Nanosystems chapter 14 | * Nanosystems chapter 14 | ||
− | [[Category:Technology | + | {{todo|add morphlense image}} |
+ | |||
+ | [[Category:Technology level III]] | ||
+ | [[Category:Nanofactory]] |
Latest revision as of 08:29, 5 September 2022
For a general overview over advanced atomically manufacturing the technology level III page.
For a less technical overview about nanofactories check out the general overview page.
- (folding)
- Assembly levels give a great aid in nanofactory design. & Tooltip preparation zone - Mechanosynthesis core - DME assembly robotics
- Design levels
- Control levels
Links to relevant quantitative details here can be found here:
- Gem-gum factory design parameters
- Nanofactory math based on continuity of throughput
- Pages with math
Contents
Basic energy balance
As carbon carrying resource material the fuel gas methane (CH4) or the welding gas acetylene (C2H2) is used. When those gasses are not burned but are being put together to products there still remains a lot of excess energy.
- heating values: CH4 55,5MJ/kg > C2H2 49,9MJ/kg > Cn 32,8MJ/kg (graphite)
As resource material the carbon carrying "exhaust-gas" carbon dioxide (CO2) in ambient air can be used too. Its like "ash" on the lowest end of the carbon combustion chain thus the heating value of zero. If it is used as building material high amounts of energy are needed.
- heating values: CO2 0,0MJ/kg < Cn 32,8MJ/kg (graphite)
Personal fabricator as stationary device
Depending on the used building material the needed or excessive energy must be taken from of fed into the power grid.
Gas lines (CH4) and atmospheric CO2 lend themselves as existing building material supply.
Related: Form factors of gem-gum factories
Personal fabricator as portable device
Huge amounts of energy cannot be provided from the small device. The resource-gasses (e.g. CH4 or C2H2 in capsules) must thus carry along enough energy for production. Simply radiating excessive heat away may slow down production significantly because of the high chemical energies involved. It may be better to balance the excess energy roughly to zero by using atmospheric CO2 as building material too. To pump high volumes of air silent medium mover metamaterials can be used.
Convergent assembly
See main page: Convergent assembly
- Convergent assembly should not be confused with with exponential assembly which is an entirely different concept.
- Convergent assembly (putting things together in a hierarchical way) is not a means to speed up production in general.
- The motivations for why to do convergent assembly are outlined on the its main page.
- The lowermost three convergent assembly steps follow naturally from the character of the technology - see assembly levels to understand this.
Covergent assembly crossing so many sizescales poses a challenge to visualizing it and making it intuitively comprehensible. Possible ways to visualize convergent assembly include:
- Distorted visualisation methods for convergent assembly – all in one picture
- Animating a fly-through with continuous scaling
Nanosystem units
Robotic manipulators
- Nanoscale: mill style robotics
- Microscale: parallel robotics – delta-bots, steward-plattforms, parallel scaras, patallel gantry bots
- Microscale to mesoscale: part streaming robotics
- Mesoscale: serial robotics – classical scara bots, classsical robot arms
- Macrocscale: dexterous tentacle style robotics (part streaming)
Threading by systems
Main page: Subsystems of gem-gum factories
- Assembly subsystem – Related: Routing levels
- Vacuum subsystem
- Coumputation subsystem
- Energy subsystem
- Thermal subsystem – Related: Thermal management in gem-gum factories
Cooling, vacuum and other logistics
- Vacuum handling
- Thermal isolation & Diamondoid heat pump system
- Medium movers for air supply
Macroscopically separating design considerations
The first two processing steps are:
- capturing resource molecules from liquid phase and purifying them by sorting mills and
- mechanosynthetic tooltip preparation.
It makes sense to do the former in a warm environment and the latter in a cold environment.
In order to avoiding freezing of solvent and minimize error rates respectively.
Macorscopic separation (possibly even in physically separate devices connected by a matter conducting wire) could be considered.
Cooling and isolation:
Although piezochemical mechanosynthesis works at room temperature cryogenic cooling will probably be employed just because
- it seems rather easy to do (see: "Diamondoid heat pump system") and
- error rates can be shrunken by many orders of magnitude.
General nanofactory design method
Given a set of "base units" for different components of the bottom-most assembly levels
their combination to form a full nanofactory unit can be determined by
first finding the relevant quantitatively or at least qualitatively (set of choices) of evaluable relevant metrics and
determine numbers of base units and branching factors based thereof.
(constraint logic programming - prolog library clpqr?) might be useful.
- condition to be fulfilled: output frequency of an assembly level == input frequency of the assembly level directly above – See: level throughput balancing
(wiki-TODO: This section needs reformulation!)
Design metrics
- ratio of manipulator to building block in volume, number of atoms or mass
Performance limits
The ultimate performance limit is determined by the accepted dissipation heat at the lower levels the maximal acceptable accelerations at the higher convergent assembly levels. Designs leading to practical speeds at human scale lie way below the performance limits.
Power dissipation is only a limiting factor at the bottom-most assembly levels. At higher assembly stages bearing area per volume drastically falls. If bearing volume is kept constant via stacking the total speeds can be dramatically increased till resonance or acceleration limits are hit. Either one accepts overpowered upper layers of the nanofactory which only can be used to their full potential when prefabricated parts are recomposed or one may deviates from the layer structure to a more complicated fractal structure for the bottom layers. (dynamic drag and breaking losses)
Threading by pre-products
Depending on whether general purpose mechanosynthetic fabricators or mill style fabricators (serial chain of tools with no spaces) are used predominantly more or less layers and channels for threading parts by are needed [?].
Speed limit at the bottom
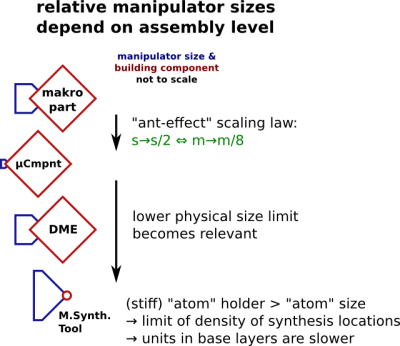
slow speed of assembly level 0: The mechanisms to assemble parts normally can potentially be smaller than the parts being assembled. Since The mechanisms to assemble minimal sized DMEs need themselves to be DMEs the mechanisms must have a similar size as the products they assemble. Since only a few atoms are added per assembly step the density of actual building sites of atomic size is rather low and consequently mechanisms at the bottommost layers are quite a bit slower than the ones above and need to be included in greater numbers.
If assembly units of an assembly level produce (pre-)products slower than the size-characteristic frequency the next higher assembly level demands one can stack assembly units and thread by finished (pre-)products. Assembly units can be stacked as long as the size characteristic frequency of the threading by mechanics is not exceeded.
Speed is also limited by the requirement to keep the rate of friction heat generation in bounds. See: Scaling laws#Speedup.
Ratios between levels
Layer and stage ratios: In any convergent assembly step a step size can be chosen. Big steps limit the maximum possible speed of the considered assembly level step but makes planning and programming more flexible and easier.
A step size that is easy on the human mind is 32 since two such steps roughtly span three (dezimal) orders of magnitude (a factor of 1000). Starting from 32nm only three steps lead to around one millimeter sized products.
Conservative estimation
There is reason to believe that steps of this magnitude won't make a nanofactory design unpractical. Todays homebuilt 3D printers can fill about 20000 voxels in one minute assuming 100 mm/second head movement and 0.3mm lateral voxel size. (20000 voxels are about the same as 32^3=32768) Since frequencies scale up with shrinking size going down doesn't change the troughput capacity.
Step sizes will probably just limit high recycling throughput but not throughput when mechanosynthesis is involved in production.
Influences of the branching factor
Branching factor: A branching factor of port area to block volume = n2/n3 leads to perfect size and frequency matching in an easy to design 3D iteration extruded 2D fractal design. Other ratios lead either to inefficient port space frequency and under used / under utilisized assembly levels or require 3D fractal designs that are more difficult to design. (There is no scale invariant design as baseline possible then)
Influences of assembly style
In any convergent assembly step one can choose from the different robotic manipulators to do the assembly. Mill style can (with the exception of the bottommost asselmbly level) have the smaller size and higher characteristic operation frequency of the lower assembly level. Single manipulator style assembly have the bigger size and smaller characteristic frequency of the upper assembly level. (Intermediate forms are possible). The choice depends on whether programmability or speed is the primary concern.
More complicated geometries
non stratified 3D fractal designs need higher convergent assembly stages (assembly level IV) to hold the structure together. They have the highest possible performance (way above practically needed levels) other limits are likely to kick in at some point. Finding a general design methodology seems to be a hard problem.For physical changes of such a design a complete microcomponent disassembly end reassembly is likely necessary.
Notes
- (TODO: list basic nanofactory subsystems as exhaustively as possible)
Maybe add these block diagrams: [1]
Related
- Productive Nanosystems From molecules to superproducts – only depicts the assembly subsystem
- Nanofactory more general introduction
- Technology level III
- Subsystems of gem-gum factories
- Thermal management in gem-gum factories
- Bottom scale assembly lines in gem-gum factories
- Tracing trajectories of component in machine phase
- Gem-gum factory design parameters
- Nanofactory math based on continuity of throughput
- Pages with math
External links
Articles from E. Drexlers Blog:
- Complete molecular manufacturing systems will have many subsystems, designed to meet many constraints
- Physical scaling laws enable small machines to be highly productive
- Josh Hall about scaling laws in productive nanosystems
External references
- Nanosystems chapter 14
(TODO: add morphlense image)