Difference between revisions of "Examples of diamondoid molecular machine elements"
m (→Assembly mechanisms: fixed link) |
m |
||
(2 intermediate revisions by the same user not shown) | |||
Line 237: | Line 237: | ||
* '''[[Stroboscopic illusion in crystolecule animations]]''' | * '''[[Stroboscopic illusion in crystolecule animations]]''' | ||
* [[Diamondoid crystolecular machine element]] | * [[Diamondoid crystolecular machine element]] | ||
+ | * '''[[Machine element]]s & [[List of machine elements]]''' | ||
* [[Nanoscale surface passivation]] | * [[Nanoscale surface passivation]] | ||
Latest revision as of 09:45, 20 May 2023
Beware of the stroboscopic illusion in crystolecule animations.
- Nominal operating speeds would be way below thermal motion speeds. (e.g. MHz instead of THz)
- Simulations are often run at abnormally high speeds to get down to reasonable simulation times. (e.g. GHz instead of MHz)
Contents
Strained shell bearings
See main page: Atomically precise slide bearing
Two structural crystolecules (the shaft and the sleeve) make up a relatively small crystolecular element here.
Specifically a diamondoid crystolecular machine element.

Crystolecule bearings are:
Just as on the macroscale bearings can come in some variations.
There can e.g. be ...
- ... no structures for axial retainment.
- ... structures for axial retainment.
Axial retainment structures can be either inside or outside the bearing.
Bearings with axial retainment they can act as thrust bearings.
There have been made examples:
- with internal axial retainment (see uppermost example animation)
- with external axial retainment (wiki-TODO: add graphic)
An internal axial retainment with helical pitch gives
a nut running on a bolt superlubricatingly.
For this case no examples have been made as of yet (2021).
A helical axle beared in a sleeve without axial retainment is also a possibility.
Such a design has been made in the context of the creation of
the drive system for the proof of concept acetylene pump.
See further below.
Strained shell gears
A main idea here is to use protruding rows of atoms as gear teeth.
Note that in the case of gears the number of atoms can not be chosen to be incommensurable
and thus the waviness of the energy potential plotted over axial rotation has
- a fixed minimal spacial period (much bigger than the one of bearings) and
- a fixed minimal magnitude (much bigger than the one of bearings).
Still as long as no snapback occurs operation can still be highly efficient.
Sulfur and oxygen have a typical bond order of two.
Oriented the right way this helps against snapback.
Sulfur is quite a bit bigger than oxygen. This can help making better (deeper) interdigitating teeth.
Sulfur is a pretty common element and for the most part a rather nontoxic element. Also nice properties.
Next up in the Chalcogen elements would be Selenium and Tellurium but these
- are quite rare
- are increasingly toxic
- increasingly deviate from desiring a bond order of two
Polonium (below tellurium) is already highly radioactive.
Gearbox
Note the links from the strained shell axles to the unstrained plate housing being sparse with gaps in-between.
Filling it in more densely to gain more stiffness without introducing huge strains that would distort the housing plates
would probably be much more difficult than manually possible. Would require some strain minimizing auto fill in algorithms.
Note that the housing walls are made not from diamond but from silicon carbide (aka moissanite) here.
Wormdrive gearbox
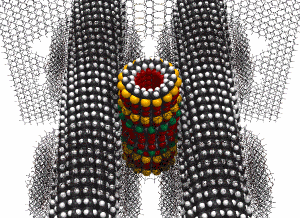
Note that at the nanoscale mechanical back-driving against much bigger transmission ratios is likely possible.
See: How friction diminishes at the nanoscale due to high reversibility of nanoscale processes.
Not that back driving wold be needed here in this particular application case.
But back-driving is useful for:
- Energy recuperation from piezochemical mechanosynthesis – See: Dissipation sharing and exothermy offloading
- chemomechanical converters when running from chemical to mechanical
- high toughness elasticity emulation converting stretching energy into broken covalent bonds – in this wiki called: chemosprings
See the assembly at the top of the acetylene sorting pump.
Mechanical circuit forks
Differential gearbox
A proof of concept example of conical teeth.
A potential problem with conical gears is
that atoms only come in one size but conical teeth widen.
The the softness of atoms can helps here.
Even if atoms behave soft on the nanoscale, the degrees of compression that are quite easily achieved at the nanoscale by forcing somewhat mismatching teeth together can correspond to what would be humongous pressures on the macroscale. The same for bearings.
Planetrary gearbox
The rollers in the proof of concept model are extremely small.
Designing that such that the simulation does not blow up must have been not an easy task.
Performance when loaded rather than free running seems rather questionable.
Teeth are not very deep so there might be slip-over already with light loads.
Reciprocative " differential gearboxes"
A whippletree should be quite simple.
Gears with bigger teeth made from multiple atoms
Only crude models with flanks totally not matching up in shape have been made so far
these would most likely be not of any practical use.
To approximate cycloid or evolvent teeth already quite large scales are necessary and
making sure atom rows stay incommensurabe such that there is no "rattle" seems like a nontrivial design task.
A graphitic (or organometallc) surface cover of a diamondoid core might be an pursuable approach maybe?
Maybe fixating a graphene sheets covering bigger teeth similar to the bonds in sandwich compounds could work??
See: Graphene sheet lining
Pumps
Acetylene sorting pump

A critically necessary processing step in advanced productive nanosystems
will be getting resource molecules out of solution into machine phase.
This was (to the knowledge of these lines author) the biggest molecular machine element
ever designed as of 2020 and a good while before.
Most critical on that design are probably channels and pistons.
How well has the hydrophobic aspect been analyzed?
That is the desire of acetylemne moleculed to go in those channels.
Hod critical is the diameter of these channels?
Synthesis of the somwhat non-stiff reciptocating etyne rods in this design wold for sure make
quite the nice challenge for mechanosnthetic cells.
Neon Pump
Background:
Especially in the early day molecular assembler concepts
one idea was to inflate graphene chambers with neon which
due to its high inertness might not disturb mechanosynthesis with open radicals too much.
For nanofactories just plain vacuum is most likely simpler.
This design features no channels and pistons but
rather moving pockets where grooves in stator and rotor meet.
As for why not the much more abundant argon was chosen this may be because:
- Argon is bigger and this less easy to filter from other stuff
- Argon is more reactive than neon and might interact more with extremely reactive open bonds.
Two piston vacuum lockout run in reverse
For now see "Vacuum lockout" for a bulk limit design that cold be converted to a model with atomic detail.
Unlike vacuum-lock-out vacuum-lock-in is not perfectly sealable for arbitrarily shaped parts to be locked in.
Which is btw quite interesting and might be linked to fundamental properties of physics.
(Just like the two options to for computer algorithms: in place overwriting (mutation) and out of place writing point to fundamental principles.)
Progressing cavity pump (PCP) aka Moineau pump
Not designed yet.
The organic shapes likely call for
- a computer doing the design.
- the design needing to be a bit bigger (but not all that big)
This would be a continuous motion atomically tight positive displacement pump,
which might be quite useful.
Hinges / Joints
Flexing universal joint

The flex-hinge principle used here might also be useful in other mechanisms.
On the page of the concept animation video: "Productive Nanosystems From molecules to superproducts"
there is a screen-capture of an unpublished scene with a belt employing that principle.
There are other issues though with this particular design though. Discussed there.
Note that this is fully hydrogen passivated. It should have quite a high chemical stability and thus be able to operate in (clean) air. There is also a version of he same model with different passivation that might be less stable and only suitable for a PPV environment. See: Nanoscale surface passivation
(wiki-TODO: Find the image of the differently passivized version (locally; it's no longer on the web it seems) – use the two images as comparison case on the to make "chemical stability" page.)
Constant velocity (CV) joints
- The classic A CV hinge – problematic
- Thomson coupling
Off axis parallel axis joints
- Oldham coupling
- Schmidt coupling
Miscellaneous
Assembly mechanisms
An ultra compact 6DOF positioning device.
Almost certainly not a practical approach.
Possible reasons for why such an ultra compact design was chosen to be modeled might be:
- Limited computer processing computing back in the day
- A focus on the now outdated concept of ultra compactly self replicating molecular assemblers
In nanofactories one would instead use molecular mills with hard coded functionality at the lowest assembly level
and high freely programmable 6DOF assembly robotics only at higher assembly levels where much more space is available
and thus things come a little closer in looks to bulk limit designs.
Other
- Superelastic springs – one is featureed in the concept animation video "Productive Nanosystems From molecules to superproducts" – (analog to capacitors in electronics)
- Friction mechanisms – none have been modelled as of yer (2021-06) – (analog to resistors in electronics)
- Clutches – (analog to transistors in electronics)
- Flywheels – (analog to inductors in electronics) – rotation speeds resulting from operation frequencies below scale natural frequencies (for reduction of friction) may limit effectiveness though
- escapement mechanisms (efficiency optimized)
- larger assembles like mechanical pulse width modulation (mechanical Buck converters)
- ...
- Wrap-spring clutch (would that work??)
Related
- Stroboscopic illusion in crystolecule animations
- Diamondoid crystolecular machine element
- Machine elements & List of machine elements
- Nanoscale surface passivation
Diamondoid and other gemstone-like crystolecular compound elements
Diamondoid crystolecular machine elements:
Exactly the same what is shown here on this example listing page, but more a discussion of their properties and such.
Bigger assemblies of several diamondoid crystolecules.
Crystolecular elements:
This page also lists various machine elements.
These are the same machine elements but beyond just ones using base materials of diamondoid structure in the narrower sense.
This would include e.g. crystolecular bearings made from a stishovite-rutile-neo polymorph as the base material.
No oxidic gemstone crystolecular elements have been modeled as of yet.
This is likely partly because the software used (Nanoenginner-1) had no support for the more difficult to handle
metallic elements (like titanium in rutile) where the limits of the construction kit analogy show increasingly pronounced.
May have also to do with molecular dynamics simulations being especially focussed on molecular biology where metals are usually only present in traces
Diamondoid and other gemstone-like crystolecules
Diamondoid crystolecules:
These are pre-produced sub-parts (sometimes non-recomposable due welding)
that the example machine elements listed here on this page are made out of.
The sleeve bearing e.g. consists of the two diamondoid crystolecules. The shaft and the sleeve.
Smaller sub components, usually structural without moving parts, sometimes seamlessly covalently weldable
Gemstone-like crystolecules (Gemstone-like molecular elements) or simply just crystolecules:
The same as Diamondoid crystolecule but not restricted to just diamondoid base materials in the narrower sense.
High level sub-classification by function
Pages about sub-classes of machine element functions (all types of gemstones):
Base material
The base material (from specific to general):