Introduction of total positional control
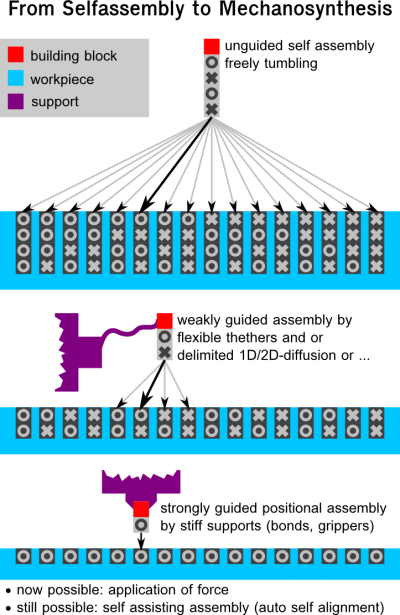
Introduction of robotic control that is unassisted by self assembly to atomically precise building block structures.
Introduction of total positional control is the step from technology level 0 to technology level I on the incremental path to APM.
(TODO: mention (and analyze) method that combines uses assembly on top of total positional control)
Contents
- 1 Reason for introduction step order
- 2 Details
- 3 Useful rigid sub micro components
- 4 Design Parameters
- 4.1 Choice of bootstrapping method
- 4.2 Few parts or many parts?
- 4.3 exclusively rotative DOFs or inclusion of translative DOFs
- 4.4 serial or parallels mechanics
- 4.5 dimensionality 3D or 2D+1D
- 4.6 rotative and translative manipulation combined or separated
- 4.7 Exoergic chain
- 4.8 Method for mechanism actuation
- 4.9 digital stepping drive or analog drive
- 4.10 Misc
- 5 Concrete example proposals for the step from T.Level 0 to 1
- 6 Goal
- 7 Related
Reason for introduction step order
Te capability to pick and place building blocks to featureless sites is a necessary prerequisite for the next step of introducing stiffer building materials since those are more featureless and thus harder to control in self assembly.
Details
Most robotic base parts consist out of structural non functional material with defined inner structure and outer limits. Thus the capability to self assemble some building material with addressable binary voxels (set or unset) suffice for the creation of robotic components or at least parts of them if the structures cannot be made big enough.
DNA-bricks are the first example providing this programmability but they are limited in size. If the limit of addressable size space can't be overcome (changing the blocks aspect ratio may help a bit) then what's needed is some form of post non binary self assembly of these or other upcoming binary voxelated bricks to larger structures. The stiffness of the whole structure must thereby be preserved.
Small scale binary voxelated bricks (of any sort) could be further assembled to rigid parts via:
- further self assembly in a second hierarchical step (reduced brownian mobility of the bigger molecules will be a problem here).
- direct robotics (taking a short-cut). For this the parts need to get into machine phase first (more about that below).
- a combination: partial self assembly followed by robotic assembly.
Using self assembly to create sturdy structures with (interlocking) hinges is not yet demonstrated and may be too hard of a problem such that after creation of the complete rigid parts robotic assembly of them seems to be a good approach.
Assuming basic rigid body robotic parts e.g. rods with eyelets for linkages (or even assembled linkages) are buildable via self assembly then to assemble them robotically e.g. via exponential assembly one needs to know their exact locations. They need to be in the machine phase.
Beside their non robotic usefulness as "molecular breadboards" Modular Molecular Composite Nanosystems (MMCS) might be useful to lay out those pre-self assembled functional components in an ordered fashion so that exponential assembly could be done.
Otherwise if one operates with the parts scattered randomly on a surface one somehow must pick the parts up check which type they are sort and store them - a rather complicated procedure. For this approach a more self replicating approach than exponential assembly might be suited better. Simple blocks could be "bulldozed" together for sorting. Bigger parts could be identified by AFM like scanning (which ruins parallelity).
Note: The more basic the structures are which can be handled robotically by the system the more productive this level I nanosystem gets (in the sense that it can produce products that can be fairly different from the system itself). If robotic control isn't voxel-brick based but rigid component based it may be more practical to introduce that capability later on.
Useful rigid sub micro components
Size adapters
If AP building blocks can be post self assembled or directly made big enough. It might make sense to create a size adapter that can be gripped by MEMS manipulators on one side and can pick and place single AP blocks with the other side. Thus spanning the top-down bottom-up gap.
The size of the smallest possible MEMS grippers and DNA-bricks aren't overlapping yet [TODO add size comparison], that is the tip radius of the grippers tend to be greater than e.g. DNA-brick sizes. So they need to be aggregated to even bigger sizes to be grippable.
To investigate:
- Can e.g. DNA-bricks be hierarchically self assembled, that is can the blocks surfaces be glued together by adding strands in a second step?
- Alternatively do complementary surfaces stick by VdW interaction even though there are no open strands (or the strands doesn't match)?
Serving plates
To make recognition of the block types easier a set of types could be self assembled to a bigger mounting plate. Designing those serving plates as boxes could provide protection from unwanted self assembly steps like when the building bock supply is depleted and the system is reloaded in liquid phase.
Building plates
Flat structures where products can be built on.
Design Parameters
Choice of bootstrapping method
Pure self assembly exponential assembly or fully fledged self replication?
[rough kewords ...]
- replicative: build volume limit -> 2D mobility
- parallel: accuracy issue - effort in parallelization of tips leaves them too un-precise ...
- bulldozing
- pros of dry operation
Mechanical and micro-mechanical systems such as AFMs and MEMS are generally very slow to slow. [TODO add quantitative numbers]
beside the problem of yet unstable tool-tips and insufficient vacuum It seems certain that they are to slow to do direct mechanosynthesis.
To investigate: Will they be fast enough to do e.g. assembly of self assembled AP bricks or bigger parts?
proto-partial-manipulator
Few parts or many parts?
To few component part types force the parts to be too generic and the resulting systems to be big slow and barely productive. There are some examples of macroscopic self replicating robot approaches that seem to suffer from this (TODO: include examples) To many component part types would require advanced not yet available systems. It still is unclear what the optimal number of part-types will be for early pre-produced block based productive nanosystems will be.
It makes sense to use some end effector adapter parts such that the parts do not all need a standard grasping interface. Thus one does not end up with having to encode placability in all pieces similar to the restriction of self-assembly: encoding place in all pieces.
exclusively rotative DOFs or inclusion of translative DOFs
Manipulators that exclusively feature rotative degrees of freedom have either non-linear motions and complex math or many bearings to create linear or almost linear motion. Mechanism to create perfect linear motion are the three dimensional Sarrus linkage and the seldom used Peaucellier–Lipkin linkage.
Cartesian mechanisms with sliderails have trivial math but may be less stiff and especially with DNA naotechnology may provide a rather bumpy ride much less accurate than a flexible hinge.
Since the surfaces of self-assembled AP blocks are far less smooth than the ones of future DMEs sliding rails for reciprocative movement may lead to risks of destructive clogging and low resolution. Linkages could make use of the already several times demonstrated edge to edge seam hinges for rotative movement instead.
Examples of rail-less robots that avoid spherical joints: Wally, Simpson, Morgan
serial or parallels mechanics
Serial mechanics means that the driving actuators ("motors") are locate in the hinges of the manipulator mechanism. With structural DNA nanotechnology this was demonstrated via shortening a DNA string that pulls on a flexible hinge like a tendon. To shorten the DNA string short DNA snippets (ogliopnucleotides) where added that can clamp a loop in the "tendon" DNA string. Since this method requires a change of dissolved oglionucleotides it is slow relative to (yet undeonstrated) electrostatic actuation (even in microfluidics). Control is also limited. The closable lengths are discrete and only a pulling action is applicable. Translative movement was also demonstrated by a remotely similar method called DNA walkers. There the amount of control is even lower but it might still prove to be very useful.
Parallel mechanics means that the actuators ("motors") are outside of the manipulator mechanism. Therefore the manipulator mechanism can be a completely passive linkage system.
Serial mechanics with electrostatic actuators in the hinges is probably impossible since the area of capacitor plates must be big enough to overpower thermal motion. The necessary area (relative to the size of the driven part!) for actuation will be smaller than in MEMS systems (comb drives) but will be still to big to be includable directly in the hinges. Also self-assemblable nano circuitry hasn't been demonstrated yet. And electrons behaving ballistic and quantum mechanical at such low scales (in contrast to mechanics) would be likely to make things more difficult - resistance may sharply change with corner angles.
Serial mechanics also leas to actuators looking more like robot arms which are due to their lower stiffness better suited for manipulation tasks on a bigger scale.
Parallel robots can provide mechanical simplicity at the cost of control complexity (inverse kinematics)
Related: rotative only or inclusion of translative
dimensionality 3D or 2D+1D
A fully three dimensional manipulator system has either complex mechanics or complex control.
A two dimensional assembly system may make the manipulator design much simpler. To erect a 3D structure afterwards some post processing manipulation will be needed. For more blocky structures layer by layer coplanar extrusion might work - like an inverse tertis. For more filigree structures a method like erecting superhuman scale trussworks without a crane might work.
rotative and translative manipulation combined or separated
To simplify manipulator design further rotation may be decouplable from translation. A separate rotator mechanism may be usable for rotation in the main directions (100) (110) (111).
Exoergic chain
From the blocks creation to their final destination they have to first get bound into machine phase then have to be picked up and finally be placed down. To archive this either the binding strengths has to strictly monotonically increase from step to step (an exoergic chain) or sterical means have to be employed. ...
When robotically assembling self assembled robotic parts it may be necessary to temporarily pin down levers to prevent them from spinning on their axles and rip them loose when putting them in use.
Method for mechanism actuation
Electrostatic
Todays most advanced nanotechnology is electronics. Driving mechanisms with electrostatic forces is thus an obvious route. Electric fields generated by microelectronics acting on a AP brick structure or an other type of structure in machine phase provide less degrees of freedom than a mechanical gripper but are considerably faster.
To keep the complexity of the mechanical mechanisms low the number of input channels must be kept as high as possible. Since the electric contacts still are rather big compared to AP building blocks one could create mechanical signal collector bundles crossing the electrodes and broadcasting reciprocative movement to a number of mechanisms.
Self assembled AP blocks may be (and probably are) electrically isolating.
Still with strong electric fields local polarizations may be induced and kind of an "stand up hair effect" could be used as driving method.
To investigate: feasibility of this approach.
If the blocks need to be made dielectric or charged to be effected by the field:
To investigate: Can blocks/block structures be made dielectric or charged sufficiently?
To use electric fields as input the block structures need to provide at least one internal 1D degree of freedom which can be compressed to 0D (machine phase). To investigate: How to create minimal sized block structures for mechanical or electrostatical actuation that are productive and capable of structural copying or self replication? The proto-mechanism problem.
Pressure
[Todo: add ref]
digital stepping drive or analog drive
Using a stepping drive means that in effect a local memory must be kept - this means more complexity in hardware. An analog drive may not have sufficient resolution if thermal motion is barely overpowered.
Misc
With basic AP blocks only very simple mechanisms will be buildable.
To be usable for somewhat functional robotic applications the blocks need to fulfil some criteria:
To investigate:
- Can an axle bearing system be built that runs non self destructively with sub block-size precision?
- Can two blocks be connected with a edge to edge hinge? (similar to the hierarchical assembly question)
- Can the blocks bind strong enough together to avoid falling apart when actuated?
- Are the surfaces of DNA-bricks made with half strands, that is are there surfaces smooth ore more like a hairy ball) [TODO dig out the known answer]
Concrete example proposals for the step from T.Level 0 to 1
[TODO to myself: add the one I've archived] technology level I
For a partial self replicating system with minimal complexity following components might suffice:
- (electrostatic) actuators of sufficient force to counter thermal noise (-> not smallest scale)
- mechanical broadcast channels to ...
- active locking of mechanical states or if unavoidable (lack of inputs, ...) ratchets
- DEMUX (depending on broadcast channel length and photo-litographic input size this may be avoidable in favour of multiple 4? inputs) (basically nano-mechanical logic here)
- simple parallel manipulator(s) (if it simplifies the design they may be split up and specialized for different DOFs?)
- gripping or expulsion mechanism (exploiting self assisted assembly)
While making assembly easier more complex pre-built base parts can reduce the productivity of a system.
If it proves too difficult to produce AP scaffolds with macroscopic long range order (self assembly in a temperature gradient?) Two stage two stage exponential assembly may solve the problem where the upper layer is built from MEMS with linear DOFs too.
Goal
Related
- Thermally driven assembly
- Locking mechanisms
- Mechanosynthesis. Usually mechanosynthesis refers (beside positional control) to formation of covalent bonds by applying force. This will only be introduced with the next step to stiffer materials which allow true atomic precision in placement.
- Bootstrapping methods for productive nanosystems
- Self replication