Intuitive feel
This is an introduction to the character of robotic work in the nanocosm.
It should deliver some intuitive feeling of how things work down there.
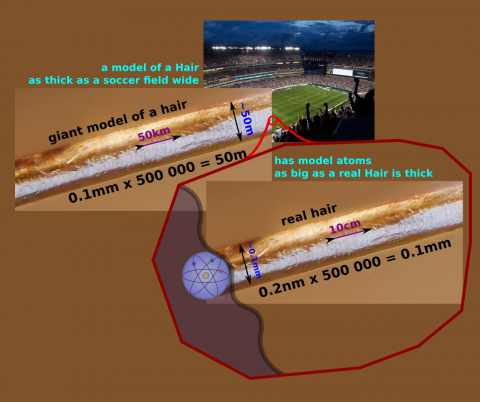
Contents
- 1 How big is an atom?
- 2 How does it feel when you grab two atoms and rub them against each other?
- 3 Speeds of motion in nanorobotics
- 3.1 The incredible rate things zap past their surroundings (just driven by temperature)
- 3.2 Assembly by mindlessly throwing parts together at ridiculous rates
- 3.3 Use of thermally driven assembly to get away from thermally driven assembly ASAP
- 3.4 The smaller the more productive
- 3.5 Motions in the far term goal of advanced nanofactories
- 4 What happens when you let go of a building block?
- 5 Scaling laws
- 6 The feel of AP Products
- 7 Bonding energies - Tensile strengths - Stiffnesses
- 8 Further
How big is an atom?
Atoms are quite small but they are not as ridiculously small as people usually say. If a hair (0.1mm) would be the width of a soccer field (~60m) an atom would be roughly the size of a hair. Carbon is about 0.2nm or 2Å in size that makes roughly five atoms per nanometer. When hierarchically building up building structures one can quickly fill up this size gap.
Relative distances in the other (astronomic) direction are vastly greater. If the planetary orbit of our outermost planet Neptune (which can technically be reached in years) where the size of a hair the nearest stars would lie beyond ~1km and the Milky Way would be ~1000km thick at our location. The next galaxies would start at the diameter of our sun ~1000000km then still follows the unimaginable size of intergalactic voids, the observable universe and the universe extrapolated to our "now" of which we now little by now.
How does it feel when you grab two atoms and rub them against each other?
First I should note that trying this out for real is actually possible for quite a while now (as unbelievable as it may sound). To feel atoms you grab the end of a robot (you shake hands with it). A tiny needle with a single atom at the tip is then made to move exactly like your hand just on a lot smaller scale. When the topmost atom on the needle tip starts to touch an atom on a surface the robot arm pushes back just as the surface pushes back on the needle albeit with a magnified force big enough for you to conveniently feel it. This is called force feedback (commonly known from car racing games).
Two analogies that might convey what it feels like best are:
- rubbing soft slippery fish or water soaked gummy bears against each other
- moving two magnets past each other in repulsive (but sometimes also attractive) configuration
Moving the robot arm in and outward you can check out softness and moving sideward you can check out slipperiness.
Slipperiness
Atoms are ridiculously slippery. Like the moon orbiting the earth there's basically no friction. If certain conditions are met this low friction can be retained for larger contact areas than just the single atom on the tip of our probing needle. One condition is that the atomic ripples on a touching pair of larger surfaces must not interlock like matching egg-crates. If this and a few other things are met there is extremely low friction. It is called the superlubrication phenomenon and it has enormous potential for technical usage in slide bearings of all kinds.
Softness
So how does it feel to break a single bond between two atoms? Since I can't let you pull on this robot arm over the web lets turn the robot arm facing downwards and tie an empty plastic bottle onto it in which we will later fill some water. We can also use a simple coil spring instead of the robot arm giving force feedback
For realism we can make the robot arm behave exactly as stiff as the bond between two atoms. Caution! Please do not mistake stiffness with force. Stiffness is how much the force grows per the length you pull. A bond between two atoms obviously has only a tiny force but this force builds up on a tiny distance. Thus while the robot arm needs to magnify both force and length the stiffness of the bond turns out to be in the right size such that the robot arm can simulate the it 1:1.
Now here's a quiz: Assuming you fill half a liter of water into the plastic bottle how much will the robot arm simulating the stiffness of a bond between two carbon atoms in diamond give (very roughly)
A:~1mm ☐ B:~1cm ☐ C:~1dm ☐
Hidden solution:
- A bond between two carbon atoms in (C-C bond) in diamond has a (maximum) spring constant of: k = 440N/m =~ 450g/cm.
Thus half a liter of water which makes 500g bends the setup ~1cm so the answer is B:~1cm ☒. That feels pretty soft to the hand. - halving the size -> halves the stiffness ... this is an instance of a scaling law of whom you'll here a lot here
- Just remember: The smaller things are the floppier they become. Even diamond one of the strongest materials in existence feels pretty soft at the scale of single atomic bonds.
Speeds of motion in nanorobotics
Today it's general education that temperature is equivalent to the speed of motion of particles at the atomic scale. If you unfamiliar with this "thermal motion" also known as "brownian motion" I suggest you read up on this elsewhere (e.g. wikipedia) before continuing here.
The incredible rate things zap past their surroundings (just driven by temperature)
Thermal motion at the nanoscale is pretty incredible.
Small single molecules zip around at thermal speeds of a few hundred meters per second. That's about the speed of sound. When we scale up size by our usual magnification factor of 500.000 to make model atoms (say water molecules) have the diameter of a human hair and when we keep the flow of time unchanged then those hair sized molecules zip around with more than half the speed of light.
But since those water molecules are densely packed they do not move in long straight lines.
- In liquid phase (e.g. water) they move in twisty paths with curve radii of about their own size.
- In one atmosphere gas phase (e.g. air) they move about 250 times their size (the mean free path length) before colliding and making a more or less U turn. In the 500,000 times scaled up model those U-turns are executed at near the speed of light every 2.5 centimeters (250 x 0.1mm).
Note that molecules in a liquid or gas that are not bond to a crystal run apart quantum-blurrily quite quickly. So a "soup" of a superposition of all possible collision-histories is a better picture for fluids and gasses.
Assembly by mindlessly throwing parts together at ridiculous rates
Given this situation it becomes very obvious that in a liquid environment that is densely packed with other solvent molecules (e.g. water) solvated molecules meet a lot of other solvated molecules in a very short amount of time. Bigger more massive molecules like proteins ("puzzle piece molecules") move slower but collision rates are still very very high.
This is why puzzle piece shaped proteins molecules in biological systems can "assemble themselves" into their intended products. Via their random collisions they just mindlessly try all possible places they could bond to in very very fast succession. It's mindless trying like having toddlers that do not yet grasp that cubes do not fit through round holes do the assembly job but since it's done so fast (like brute force computer algorithms) useful things can be assembled nonetheless.
The technical term for this method of assembly is "self assembly" but here we'll call it "thermally driven assembly" which captures the meaning better. On the day to day macroscale this method of assembly is usually not applied for practical purposes due to its ridiculous slowness and requirement of parts fitting together like a sticky puzzle. Fully grasping the process how it happens at the nanoscale at an intuitive level may be impossible due to the vast number of trials until the final successful bonding reaction. (TODO: investigate better visualization methods) There are beautiful CG videos of molecular biology that use fake motions mo make it comprehensible (TODO: add link).
Use of thermally driven assembly to get away from thermally driven assembly ASAP
Thermally driven assembly is the predominant form of assembly in biological systems. Thermally driven assembly of increasingly arfificial molecules will be (and already is!!) a very useful tool for walking the initial steps of the path to advanced nanofactories. But as it turns out in an advanced nanofactory (the far term goal) it makes much more sense to actually constrain / suppress thermal vibrations and take care of the transport oneself in a fully controlled and less mindless fashion.
The idea of working towards a point where we deny the help of thermal motion (shunning the teachings of nature) but doing assembly tightly controlled and guided instead has received harsh criticism in the past. It was and still is often misunderstood as a misunderstading of the real nature of the nanocosm.
But there actually is an example where we already succeeded with the suppression of thermal noise. Nanoelectronics. In microchips we've already learned to suppress thermally caused electrical noise without even noticing it since it just gradually got more difficult.
The two necessary requirements for thermal noise suppression are the same that we used to get away from analog technology namely:
- error margins and
- error correction
Now we use mostly digital electronics.
Given that electrons start to behave strongly quantum-mechanically in the nanoscale (quantum blurriness and thermal motion can often be treated in a common fashion) -- which stands is in stark contrast to nanomechanical nanomachines -- this is even more of a feat. We where not forced to switch some sort of probabilistic electronics (whatever that would be). Since much less quantum mechanical in behavior advanced nanomechanical systems will have even less reason to work in a purely probabilistic fashion.
The smaller the more productive
While size goes down speed goes up. A good example in nature is the increasing wing flapping rate seen in birds and insects.
By naively scaling down a current day 3D-printer by a factor of 500.000 (just for illustration - not a serious proposal) it becomes 500.000 times faster. A typically time for 3D printers to print parts that have about the mass of the printer itself is on the order of 10 hours. This shrinks down to just 0.72 seconds.
Now a single shrunk down printer won't produce much but imagine the whole volume of the original non-shrunk printer filled up with shrunk down printers. This would then produce the macroscale printers own mass in less than a second.
In a serious advanced nanofactory design the time to produce the production machinery's own mass can become even smaller due to better materials, lower friction, smaller size steps, to name a few reasons. For a good intuitive feel about the production rate imagine products shooting out like rifle bullets.
I fact the time to produce production machinery's own mass can become so short that the products that can be produced at the nanoscale cannot be fed out fast enough at the macroscale anymore. Getting even remotely near there would require impractical levels of cooling.
Solution: One humbly accepts not to get the full crazy level potential of nanoscale production machinery and is content with just more than practical levels of productivity.
To do this one does not fill up the whole volume with productive nanosystems. One abandons the concept of clouds of molecular assemblers. Instead one integrates everything in a thin chip. A nanofactory. For details check the main article: Macroscale slowness bottleneck
Even in the case when one really wants to push the limits (there's likely military interest here) its likely that a highly advanced fractal nanofactory that is a little thicker is the best solution. For a continuously running device the cooling facilities then are likely much bigger than the productive device itself. The production becomes highly inefficient and turns a lot of energy into heat. Still there is the fundamental specific acceleration limit which cannot be exceeded. This is the point where no known material would not break from the acceleration loads.
Motions in the far term goal of advanced nanofactories
Assembly in an advanced nanofactory will resemble more of a factory assembly line far away from any similarity to biological systems. All the machinery will usually run much slower than the thermal motions (about at least a factor of 1000) but since every try is a hit (for all practical purposes) the production throughput can be the same or higher than the one of natural bio-systems that work with thermally driven assembly.
In rare occasions one might want to let go of molecules or crystolecules in an advanced nanosystem. Thermal motion for bigger crystolecules in a vacuum under gravity are statistically distributed throwing parabolas. Single molecules show significant quantum blurring when released.
- Envelope of throwing trajectories with same speed
- Throwing trajectories with various speed in same direction
What happens when you let go of a building block?
Let's consider an somewhat unusual fall experiment. A small gripper let go of a building block. Simple? See if you answer right.
Scaling laws
They describe what changes when one goes down the scale. E.g. that magnetic motors become weak but electrostatic ones strong. More details can be found at the scaling laws main page.
The feel of AP Products
AP products though robotic and gemstone like in the nanocosm are not necessarily cold hard and robot like to the human senses. Emulated elasticity can create any form imaginable with gradients from soft to hard. It isn't an easy to attain property but it is an highly desirable one and will emerge at some point.
Bonding energies - Tensile strengths - Stiffnesses
(TODO: Add the same info table as on VdW force page)
[Todo: Add table - make it visualizable for covalent bonds and VdW bonds]
[Todo: show surface area thats VdW ashesion is energetically equivalent to one covalent bond - related: Form locking]
Further
- Periodic table of elements
- acceleration limits
- jumping building blocks
- Why nanomechanics is barely mechanical quantummechanics
- Video Playlist: The Shape of Atoms and Bonds (By "Learn Hub")
- Distorted visualisation methods for convergent assembly
- Scaling laws