Difference between revisions of "Stiffness focusing"
m (removed stub marker) |
(→Math of simplified 1D problem: added notes on limits to the formula) |
||
Line 39: | Line 39: | ||
k_{total} = \left[\sum_{i=1}^{l} \frac{L_i}{E_i A_i} + \sum_{j=1}^{n} \frac{1}{k'_A{_j} A_j} + \sum_{k=1}^{m} \int_{z_{k,1}}^{z_{k,2}} \frac{dz}{E_k A_k(z)}\right]^{-1} | k_{total} = \left[\sum_{i=1}^{l} \frac{L_i}{E_i A_i} + \sum_{j=1}^{n} \frac{1}{k'_A{_j} A_j} + \sum_{k=1}^{m} \int_{z_{k,1}}^{z_{k,2}} \frac{dz}{E_k A_k(z)}\right]^{-1} | ||
</math> | </math> | ||
+ | |||
+ | This formula does not take into account some simple things like say 90° turns of a support structure. <br> | ||
+ | One could extend for that but at some point numerical finite element simulations are a better approach beyond <br> | ||
+ | some crude initial back on the envelope estimations. <br> | ||
== Variables and Units == | == Variables and Units == |
Latest revision as of 12:28, 19 November 2024
(wiki-TODO: Add image illustrating the stiffness focusing effect and math method for calculation)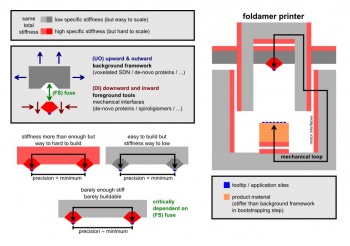
Going along the kinematic loop usually with monotonously in area shrinking cross section (finally through conical tip)
the same force gets focused on smaller and smaller areas thereby increasing the pressure towards really High pressure.
There is more to this though.
An interesting for piezochemical mechanosynthesis highly relevant question is
what the the absolute stiffness at the tip in terms of N/m (as SI units) will be.
With systems built up out of heterogeneous materials there are different specific stiffnesses (Young modulus).
For every specific stiffness and cross section at some point in the kinematic loop
there is an equivalent absolute stiffness at the very tip (with defined areal cross section).
To get the absolute stiffness at the very tip of the SPM probe one
calculates the equivalent stiffnesses of fine layers (or sections with constant cross section)
an sums up their inverses (summing up compliances). Possible infinetesimally i.e. integration.
This physical process and modeling for it is what we shall call here in this wiki
"stiffness focussing"
A higher area can make up for a lower stiffness (to a degree)
So e.g. what higher upstream the kinematic loop would only suffice for
topological atomic precision can further downstream the kinematic loop (towards tip)
suffice for positional atomic precision.
To a degree means there are obviously limits.
E.g. protein assemblies with matching up complementary surfaces that make their side chains crystallize
may be able to focus to enough stiffness for positional atomic precision with an insets
crystolecule core final tip of the kinematic loop.
But just linking proteins together more covalently without matching up surfaces will not provide sufficient stiffness
for positional atomic precision. It may still provide enough constraints for other tasks like tether assisted assembly.
Contents
Math of simplified 1D problem
Formula for stiffness at the tip:
The total absolute stiffness [math]k_{total}[/math] can be expressed as:
[math]
k_{total} = \left[\sum_{i=1}^{l} \frac{L_i}{E_i A_i} + \sum_{j=1}^{n} \frac{1}{k'_A{_j} A_j} + \sum_{k=1}^{m} \int_{z_{k,1}}^{z_{k,2}} \frac{dz}{E_k A_k(z)}\right]^{-1}
[/math]
This formula does not take into account some simple things like say 90° turns of a support structure.
One could extend for that but at some point numerical finite element simulations are a better approach beyond
some crude initial back on the envelope estimations.
Variables and Units
- Absolute stiffness [math]k[/math]: [N/m]
- Bulk Young's modulus [math]E[/math]: [Pa] = [N/m²]
- Specific interface stiffness [math]k'_A[/math]: [(N/m)/m²] = [N/m³]
This represents "absolute stiffness per area".
Also known as "interface stiffness parameter".
Product with area gives the absolute interface stiffness [N/m].
Back to tip interface stiffness (sensible?)
[math] k'_{tip} = \frac{k_{total}}{A_{tip}} [/math] Where:
- [math]k'_{tip}[/math]: [(N/m)/m²] = [N/m³] specific interface stiffness at tip
- [math]k_{total}[/math]: [N/m] previously calculated absolute stiffness
- [math]A_{tip}[/math]: [m²] tip area