Difference between revisions of "Foldamer technology stiffness nesting"
m (→Technologies form least stiff most scalable to most stiff least scalable) |
m (→Technologies form least stiff most scalable to most stiff least scalable) |
||
Line 18: | Line 18: | ||
Side-note on scalability: <br> | Side-note on scalability: <br> | ||
− | Spiroligomers may be scalable in the quantity of them synthesizable. <br> | + | Spiroligomers may be scalable in the quantity of them synthesizable. (Relevant for early material type products.) <br> |
− | + | Though here we look solely at scalability in terms of selfassembly with [[termination control]]. <br> | |
== Combining of technologies to get max scalability and max stiffness where they matter == | == Combining of technologies to get max scalability and max stiffness where they matter == |
Revision as of 11:50, 17 June 2024
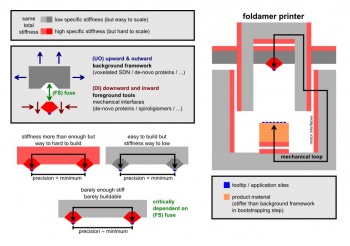
The idea here is to combine the different foldamer technologies to get the best of all the worlds.
There are various forms of foldamer technology under development.
A pattern that one may spot here is that …
– … the most scalable technologies feature the least stiffness while
– … the least scalable technologies feature the most stiffness
⚠ Scalability here does not mean mere quantity but only the quantity for which full termination control can be achieved.
Contents
[hide]Technologies form least stiff most scalable to most stiff least scalable
- 3D structural DNA nanotechnology - all mere topological atomic precision
- de-novo proteins - positional atomic precision of stiff backbone core
- not so for the floppy side-chains => origin of "fat fingers" - spiroligomers and stiff artificial stiff side-chains - positional atomic precision
- small core crystolecules - if direct path gets so far on it's own - positional atomic precision
Side-note on scalability:
Spiroligomers may be scalable in the quantity of them synthesizable. (Relevant for early material type products.)
Though here we look solely at scalability in terms of selfassembly with termination control.
Combining of technologies to get max scalability and max stiffness where they matter
The bigger-than-inter-atom-spacing-thermal-wiggles of a 3D structural DNA nanotechnology background framework
that features merely topological atomic precision
may eventually even statistically cancel out to give positional atomic precision
of the nested stiffer de-novo protein core and
of the further nested stiff artificial side-chains on that protein.
Though achieving a wiggle-reduction all the way down to positional atomic precision in one swoop is not strictly necessary
to get to a next gen better material techology enabled by semi-positional assembly.
It's much more likely that things will evolve more gradually.
Maybe this idea is more to treat conceptually.
Same in other words: Positional atomic precision (or near that) is only eventually needed between the workpiece and the tool-tip.
There is no need for positional atomic precision in the much larger "background framework/spacefame".
The background framework merely feature topological atomic precision.
Even with quite a bit of tolerable errors.
A protein core in a 3D structural DNA background framework matrix features a stiffness not defined solely by the elastic moduli,
but rather by the interface surface area too. This area needs to be factored in to get the total stiffness.
The conceptual math trick here is to look at absolute stiffnesses in N/m
rather than area specific stiffnesses in (N/m)/m² i.e. elastic modulus.
Then look at the chain that forms parts or the whole of a kinematic loop.
The incurred challenge
The various different kinds of technologies need to me made compatible in the sence of connectability.
The formable connections need to feature a stiffness that is not notably lower than the stiffness of the
less stiff technology of the pair to connect.
Beside the huge experimental problems with that there's also not much software around for that (as of mid 2024).
The MSEP project has a focus on that cross technology mergability / connectability.
Alternate names
- Matryoshka doll stiffness nesting
- Onyon stiffness nesting