Difference between revisions of "Friction in gem-gum technology"
(Added info about main sources of friction, main ways to reduce them, and when stop to stop to optimize) |
m (→External links) |
||
(10 intermediate revisions by the same user not shown) | |||
Line 11: | Line 11: | ||
* '''Yes, It is true that physics changes when the size-scale changes.''' <br>But who says it changes for the worse when it comes to [[macroscale style machinery at the nanoscale]]? | * '''Yes, It is true that physics changes when the size-scale changes.''' <br>But who says it changes for the worse when it comes to [[macroscale style machinery at the nanoscale]]? | ||
* '''Yes, It is true that [[rising surface area|surface area grows with shrinking structure sizes]], and that this contributes to friction.''' <br>But there are other effects that overcompensate growing surface area and these are very often overlooked. | * '''Yes, It is true that [[rising surface area|surface area grows with shrinking structure sizes]], and that this contributes to friction.''' <br>But there are other effects that overcompensate growing surface area and these are very often overlooked. | ||
− | * '''Yes, It is true that unlike diffusion transport there is friction all the time along the whole way.''' <br>But it's often overlooked that diffusion must devaluate chunks of energy at its "pit-stops" to prevent transport from running backwards and that the "change money" energy that gets left over at these "pit-stops" cannot be kept | + | * '''Yes, It is true that unlike diffusion transport there is friction all the time along the whole way.''' <br>But it's often overlooked that diffusion must devaluate chunks of energy at its "pit-stops" to prevent transport from running backwards and <br>that the "change money" energy that gets left over at these "pit-stops" cannot be kept for later usage. <br><small>Whereas in [[machine phase system]]s keeping and reuseing the energetic change money may be possible.</small> |
− | * '''Yes, It is true that there is no natural example of macro style machinery at the nanoscale (similar to the one proposed).''' <br>But concluding from that that it's not possible or a worse solution is a fallacy. There are plenty of human invented things that exceed capabilities of nature by orders of magnitude. To give just a few examples: Bicycles, combustion engines (spaceships), copper wires (superconductors), wheels and streets, ... | + | * '''Yes, It is true that there is no natural example of macro style machinery at the nanoscale (similar to the one proposed).''' <br>But concluding from that that it's not possible or a worse solution is a fallacy. <br>There are plenty of human invented things that exceed capabilities of nature by orders of magnitude. <br>To give just a few examples: Bicycles, combustion engines (spaceships), copper wires (superconductors), wheels and streets, ... |
− | * '''Yes, It is true that MEMS (microelectromechanical systems) have high friction (and | + | * '''Yes, It is true that MEMS (microelectromechanical systems) have high friction (and bad wear from "stiction").''' <br>But in case of MEMS this is due to MEMS not having atomically precise [[superlubricity|suberbublicating]] bearings but instead <br>having a really bad signal to noise ratio in their geometry due to them being manufactured top-down. |
− | = | + | = Main sources of friction and countermeasures = |
Friction in [[gem-gum-tec|gemstone based nanomachinery]] is mainly caused by: | Friction in [[gem-gum-tec|gemstone based nanomachinery]] is mainly caused by: | ||
* (1) band-stiffness scattering drag and | * (1) band-stiffness scattering drag and | ||
* (2) shear-reflection drag | * (2) shear-reflection drag | ||
− | Source: [[Nanosystems]] 10.4.6. Mechanisms of Energy dissipation f. Summary | + | Source: [[Nanosystems]] 10.4.6. Mechanisms of Energy dissipation f. Summary <br> |
− | + | ||
{{todo|find and add an intuitively comprehensible explanation for these two [[phonon interaction based dissipation mechanisms]]}} | {{todo|find and add an intuitively comprehensible explanation for these two [[phonon interaction based dissipation mechanisms]]}} | ||
+ | |||
+ | Furthermore there are energy dissipation mechanisms that are specific to reciprocative motion. <br> | ||
+ | '''See page: [[Reciprocative friction in gem-gum technology]]''' | ||
== Tuning for superlubricity against band-stiffness scattering drag == | == Tuning for superlubricity against band-stiffness scattering drag == | ||
Line 42: | Line 44: | ||
'''Increasing compenslow can reduce losses from friction by many orders of magnitude.''' <br> | '''Increasing compenslow can reduce losses from friction by many orders of magnitude.''' <br> | ||
− | + | ||
− | Only the assembly motions are slowed down but | + | === Limits to optimization by increase of "compenslow" === |
+ | |||
+ | At some point friction from fast transport motions becomes relevant.<br> | ||
+ | Only the assembly motions are slowed down but assembly motions make up most of the distance the robotics travels. <br> | ||
+ | Once transport motions get similar in length to the assembly motions. Increasing compenslow is no longer a viable optimization option. | ||
+ | |||
+ | Also: | ||
+ | * the more parts are assembled per [[assembly cycle]] across an [[assembly level]] | ||
+ | * the more there is potential for reduction of friction by increase of compenslow across that assembly level | ||
== Don't over-optimize friction way below mechanochemical losses == | == Don't over-optimize friction way below mechanochemical losses == | ||
Line 52: | Line 62: | ||
already leads to some minimal compenslow.</small> | already leads to some minimal compenslow.</small> | ||
− | For systems that do not perform any mechanochemical conversions like e.g. [[microcomponent | + | For systems that do not perform any mechanochemical conversions like e.g. [[microcomponent recomposer]]s <br> |
losses from friction may become the remaining dominant factor. Relevant in the context of [[recycling]]. <br> | losses from friction may become the remaining dominant factor. Relevant in the context of [[recycling]]. <br> | ||
So here going all out on minimizing friction may really pay off. | So here going all out on minimizing friction may really pay off. | ||
− | = | + | = Employing scaling laws against friction = |
+ | '''Overcompensating increased friction from increased bearing area'''<br> | ||
'''See main page: [[How friction diminishes at the nanoscale]]''' | '''See main page: [[How friction diminishes at the nanoscale]]''' | ||
Line 79: | Line 90: | ||
* In both cases speed falls linearly with the number of bearing layers. <br> This gives simultaneously a linear increase (more bearing area) and a quadratic fall (less bearing speed) of friction losses. <br> That is: overall a linear fall of friction losses. | * In both cases speed falls linearly with the number of bearing layers. <br> This gives simultaneously a linear increase (more bearing area) and a quadratic fall (less bearing speed) of friction losses. <br> That is: overall a linear fall of friction losses. | ||
---- | ---- | ||
− | * The first case is relevant for the bottom-most layer of [[convergent assembly]] in [[gemstone | + | * The first case is relevant for the bottom-most layer of [[convergent assembly]] in [[gemstone metamaterial on-chip factories]] |
* The second case is relevant for higher up layers of [[convergent assembly]] where larger scale bearings are possible. | * The second case is relevant for higher up layers of [[convergent assembly]] where larger scale bearings are possible. | ||
Line 348: | Line 359: | ||
* [[Crystolecule]]s | * [[Crystolecule]]s | ||
* [[How friction diminishes at the nanoscale]] | * [[How friction diminishes at the nanoscale]] | ||
+ | * [[Atomically precise bearings]] – especially [[Atomically precise slide bearing]]s | ||
+ | * '''[[Mesoscale friction]]''' | ||
[[Nanosystems]] – Chapter 7 – Energy Dissipation – (page 161 to 190) | [[Nanosystems]] – Chapter 7 – Energy Dissipation – (page 161 to 190) | ||
+ | ---- | ||
+ | * [[Losses from mechanochemical reactions]] | ||
+ | ---- | ||
+ | * '''[[Wear]]''' | ||
== External links == | == External links == | ||
Line 360: | Line 377: | ||
* Wikipedia: [https://en.wikipedia.org/wiki/Rotational%E2%80%93vibrational_spectroscopy Rotational–vibrational spectroscopy] | * Wikipedia: [https://en.wikipedia.org/wiki/Rotational%E2%80%93vibrational_spectroscopy Rotational–vibrational spectroscopy] | ||
* Wikipedia: [https://en.wikipedia.org/wiki/Infrared_spectroscopy Infrared spectroscopy] & [https://en.wikipedia.org/wiki/Thermal_infrared_spectroscopy Thermal infrared spectroscopy] | * Wikipedia: [https://en.wikipedia.org/wiki/Infrared_spectroscopy Infrared spectroscopy] & [https://en.wikipedia.org/wiki/Thermal_infrared_spectroscopy Thermal infrared spectroscopy] | ||
+ | ---- | ||
+ | * https://sci-nanotech.com/index.php?thread/43-a-closer-look-at-friction-in-cog-gear-style-stiff-nanomachinery/ | ||
= References = | = References = | ||
<references/> | <references/> |
Latest revision as of 15:21, 6 October 2024
(wiki-TODO: This page needs major cleanup - several parts need to be merged and completed and factored out)
Up: Friction
Macroscale style machinery at the nanoscale has in the past received some seriously bad reputation because it comes with a bunch of mental trapdoors that led a a number of very smart reputational and vocal people to bad conclusions. One of these bad conclusions is that macroscale style machinery at the nanoscale would lead to exorbitant amounts of friction. A very wrong conclusion, as I will try to show below. (There are other misled criticisms to the idea beside the false conclusion of exorbitant friction. For a discussion of those you may want to check out the main page about macroscale style machinery at the nanoscale.)
Contents
- 1 Dodge the trapdoors
- 2 Main sources of friction and countermeasures
- 3 Employing scaling laws against friction
- 4 Quantitatively (Math and Numbers)
- 5 Numbers from papers -- less safe (since more optimistic)
- 6 TODO update chapters below
- 6.1 Flawless surfaces drop friction significantly
- 6.2 Evolved molecular biology is not a proof that diffusion transport is the ideal solution with minimal losses
- 6.3 Proposed machine speeds are WAY below speeds of thermal motion
- 6.4 Typical operation frequencies
- 6.5 Less soft nanomachinery => less drag
- 6.6 Related
- 6.7 External links
- 7 References
Dodge the trapdoors
- Yes, It is true that physics changes when the size-scale changes.
But who says it changes for the worse when it comes to macroscale style machinery at the nanoscale? - Yes, It is true that surface area grows with shrinking structure sizes, and that this contributes to friction.
But there are other effects that overcompensate growing surface area and these are very often overlooked. - Yes, It is true that unlike diffusion transport there is friction all the time along the whole way.
But it's often overlooked that diffusion must devaluate chunks of energy at its "pit-stops" to prevent transport from running backwards and
that the "change money" energy that gets left over at these "pit-stops" cannot be kept for later usage.
Whereas in machine phase systems keeping and reuseing the energetic change money may be possible. - Yes, It is true that there is no natural example of macro style machinery at the nanoscale (similar to the one proposed).
But concluding from that that it's not possible or a worse solution is a fallacy.
There are plenty of human invented things that exceed capabilities of nature by orders of magnitude.
To give just a few examples: Bicycles, combustion engines (spaceships), copper wires (superconductors), wheels and streets, ... - Yes, It is true that MEMS (microelectromechanical systems) have high friction (and bad wear from "stiction").
But in case of MEMS this is due to MEMS not having atomically precise suberbublicating bearings but instead
having a really bad signal to noise ratio in their geometry due to them being manufactured top-down.
Main sources of friction and countermeasures
Friction in gemstone based nanomachinery is mainly caused by:
- (1) band-stiffness scattering drag and
- (2) shear-reflection drag
Source: Nanosystems 10.4.6. Mechanisms of Energy dissipation f. Summary
(TODO: find and add an intuitively comprehensible explanation for these two phonon interaction based dissipation mechanisms)
Furthermore there are energy dissipation mechanisms that are specific to reciprocative motion.
See page: Reciprocative friction in gem-gum technology
Tuning for superlubricity against band-stiffness scattering drag
Only (1) can be reduced by tuning for superlubricity till (2) gets dominant.
Maybe about x100 lower friction possible tuned vs untuned?
Cranking up "compenslow" to reduce friction overall
Both (1) and (2) can be reduced cranking up the "compenslow" design parameter.
Higher "compenslow" means an increased amount of nanomachinery that all runs at a slower absolute speed.
"Compenslow" is a portemonteau for "by more machinery compensated slowdown"
When doubling the compenslow:
- The total throughput per chip area (areal throughput density) stays unchanged!
- Friction losses are cut in half.
- The thickness of the nanomachinery layer doubles. (this is not an issue)
- the internal bearing area per chip area doubles and speeds are cut in half.
Increasing compenslow can reduce losses from friction by many orders of magnitude.
Limits to optimization by increase of "compenslow"
At some point friction from fast transport motions becomes relevant.
Only the assembly motions are slowed down but assembly motions make up most of the distance the robotics travels.
Once transport motions get similar in length to the assembly motions. Increasing compenslow is no longer a viable optimization option.
Also:
- the more parts are assembled per assembly cycle across an assembly level
- the more there is potential for reduction of friction by increase of compenslow across that assembly level
Don't over-optimize friction way below mechanochemical losses
For systems that perform piezochemical mechanosynthesis and or chemomechanical conversion
it's only sensible to tune friction down so far that losses from mechanochemical reactions become clearly dominant.
Note that the increased amount of nanomachinery that results from for standard parts specialized subsystems
already leads to some minimal compenslow.
For systems that do not perform any mechanochemical conversions like e.g. microcomponent recomposers
losses from friction may become the remaining dominant factor. Relevant in the context of recycling.
So here going all out on minimizing friction may really pay off.
Employing scaling laws against friction
Overcompensating increased friction from increased bearing area
See main page: How friction diminishes at the nanoscale
- higher throughput of smaller machinery
Halving the size of the robotics has doubles the throughput per volume when robotic keeping speeds (NOT frequencies) constant.
This means that in a naive first approximation the total bearing area of nanomchinery in a gem-gum factory is no bigger than the bearing area of macromachinery. It's desirable to deviate quite a bit from that first approximation, but as it turns out that only drops friction even further despite increasing bearing area. - power losses from friction scale quadratic with speed
that is: 1/2 the speed of the machinery => 1/4th friction power losses
The two main tricks that apply and combine these physical facts to great avail
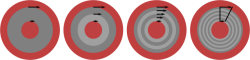
- Distribute productive activity over a lot more layers of nanomachinery
(there is more than sufficient space to do so. See multilayer assembly layers) - Distribute speed differences over multiple coplanar surfaces
(there is ore than sufficient space to do so)
- In both cases there is more then sufficient space available to do so.
- In both cases speed falls linearly with the number of bearing layers.
This gives simultaneously a linear increase (more bearing area) and a quadratic fall (less bearing speed) of friction losses.
That is: overall a linear fall of friction losses.
- The first case is relevant for the bottom-most layer of convergent assembly in gemstone metamaterial on-chip factories
- The second case is relevant for higher up layers of convergent assembly where larger scale bearings are possible.
Smaller contributions
- Bearing can be tuned for good superlubricity
- minimization of travel-distance needed per chemical synthesis operation
dissipation falls linearly with the path traveled
Minimization of travel-distance leads towards the nanofactory design and away from the molecular assembler design.
(wiki-TODO: elaborate on that)
Quantitatively (Math and Numbers)
Dynamic drag in superlubricating gemstone bearings - vs - viscous drag in liquids
There is at least 2,000.0 to 100,000.0 times less friction in gemstone bearings compared to movement at the same speed in water.
So when it comes to peak performance parameters
soft nanotechnologies and artificial synthetic biology derived from molecular biology,
is fundamentally massively inferior to gemstone metamaterial technology
Yes, this much lower friction is still more than the zero friction that is as present in diffusion transport.
But this misses a crucial point.
For diffusion transport to happen it still needs to "expend" energy (still needs to devaluate free energy).
It is just that the free energy expense need to be payed up at the pitstops (when crossing cell- and vesticle-membranes) rather than during the transport motion. (see external links)
So:
Diffusion transport driven by concentration gradients does NOT make biological nanosystems fundamentally more efficient than conveyorbelt style transport in stiff dry artificial nanosystems in a vacuum.
Associated math
Source: [1]
Rotating sphere in Water: (Source: [2])
- [math] \omega = v/R [/math]
- Drag-torque: [math] M_{flow} = -8 \pi \eta R^3 \omega [/math]
- Dissipation: [math] P_{flow} = M_{flow} \omega = 8 \pi \eta R v^2 [/math]
With: [math] \eta \approx 10 \times 10^{-3} Pa \cdot s [/math] and [math] R = 2nm [/math]
- Dissipation: [math] P_{flow} \approx 5 \times 10^{-11} v^2 W = 5 \times 10^{-11} W/(m/s)^2[/math]
Gemstone sleeve nearing: (Source: [3])
- [math] P_{drag} = 5.8 \times 10^{-16} W/(m/s)² -- \Delta k_a / k_a = 0.003[/math]
- [math] P_{drag} = 2.7 \times 10^{-14} W/(m/s)² -- \Delta k_a / k_a = 0.4 [/math]
Ratio:
- [math] P_{flow} / P_{drag} \approx 2000 … 100000[/math]
Despite superlubricity dynamic drag can be significant
(wiki-TODO: add doublelog gnulot plot of examples)
While static friction in superlubricity falls to nigh zero,
Dynamic (speed dependent) friction can be quite significant for higher speeds.
For higher speeds and bearings that do not resort to:
- some mean of levitation ( only possible for low loads ) or
- bearing stratification ( only possible for bigger nearings )
... the friction per area can actually get quite high for higher speeds.
v=100µm/s | v=1mm/s (proposed speed) |
v=10mm/s (proposed speed) |
v=100mm/s | v=1m/s | v=10m/s |
230nW/m² to 10µW/m² | 23µW/m² to 1mW/m² | 2.3mW/m² to 100mW/m² | 230mW/m² to 10W/m² | 23W/m² to 1kW/m² | 2.3kW/m² to 100kW/m² |
- [math] P_{drag} = 23 W/(m²(m/s)²) -- \Delta k_a / k_a = 0.003[/math]
- [math] P_{drag} = 1080 W/(m²(m/s)²) -- \Delta k_a / k_a = 0.4 [/math]
Source: Nanosystems Equation (10.27) [3] --
But here calculated backwards to friction per area from friction per bearing.
Note: These are highly conservative estimates. Real values should be quite a bit lower.
Halving the linear speed (in units of m/s) quaters the friction losses.
And going down from 1m/s to 1mm/s the friction losses fall by a factor of a million (1,000,000).
More technically: Dynamic friction for crystolecules scales quadratically with speed.
Why significant dynamic drag at higher speeds is this is not a problem
Note: This section is redundant but provides a different formulation. Skip ahead if the everything so far was clear.
Worry #1: Looking at the table friction per area for small speeds like 1m/s is quite high.
Friction can be massively massively reduced by reducing the linear speed of motions (speed in units m/s NOT Hz!).
And we can totally afford to reduce the linear speed of motion in advanced productive nanosystems because all the machinery that is needed for practical levels of throughput fits in a super thin layer at the very bottom of the convergent assembly of a gem-gum factory chip.
(Reason: Higher throughput of smaller machinery - things scale favorably here)
We just need to make the bottom layer gem-gum factory chip a bit thicker
to compensate for the loss of speed and we are back at the original throughput.
(We want to do that anyway because many different specialized assembly lines need space.)
One totally can afford to slow down so much in advanced productive nanosystems like gem-gum factories
because there is plenty of space to compensate by just adding more nanomachinery.
Q: But what about the additional bearing area?
A: Yes, the total bearing area increases.
But while 10x the amount of nanomachinery gives 10x the bearing area
the friction per area falls by 100x due to 1/10th the speed.
So overall friction falls by 10x.
PS: Also note that the table above gives conservative (pessimistic) estimates on levels of friction.
Worry #2: Nanotech has a lot of surface area per volume. Won't that cause friction to become excessive?
Q: Shouldn't there be massive amounts of bearing surface area?
It's nanomachinery after all, and and for nanotechnology the surface to volume ratio gets extremely high?
A: Surface per volume is indeed high. BUT: We barely need any volume to achieve practical levels of throughput.
(Reason: Higher throughput of smaller machinery - things scale favorably here)
Looking at convergent assembly in a first naive approximation every layer has exactly the same bearing area.
So the bottom-most nanomachinery layer has exactly the same bearing area as the topmost macroscale assembly chamber.
In practice one would want to deviate form naive convergent assembly by making the bottom layer thicker,
which, as described above, only improves the situation with friction losses from dynamic drag.
As for the bearing area of the convergent assembly layers higher up:
- (1) There are only a few convergent assembly layers present (take 32nm chambers times 32 four times and you are at 32mm).
- (2) Bigger bearings can infinitesimal bearings. Again. Same trick. Area x10 & speed x1/10 => overall friction x1/10.
Highly conservative form Nanosystems (wiki-TODO: check and merge this section)
Assumed:
- A crystolecule bearing with 2nm radius and 2nm length
- Bearing stiffness k = 1000N/m
- Bearing bumpiness incommensurability: R = abs(m/(m-n)) = 10
- Bearing operating temperature: Roomtemperature 300K
The dominant power loss contributions (Nanosystems 10.4.6.f.) give:
- P = 2.7*10⁻14 W / (m/s)^2 -- (for Δka/ka = 0.4) or
- P = 5.8*10⁻16 W / (m/s)^2 -- (for Δka/ka = 0.003)
So how much waste heat would one get for a reasonable desktop gemstone metamaterial on-chip factory?
It is not calculated in Nanosystems since energy recuperation inefficiencies
- in force applying mechanosynthesis and
- "covalent welding" block assembly
likely dominates.
But let's confirm that:
The proposed nanofactory convergent assembly system architecture (Nanosystems Table 14.1.)
lists (as reasonable) a few times 10^17 units at the lowest assembly levels.
Nanosystems provides no info about how many bearings per unit to assume.
But Let's assume 100 bearings per unit. This kinda seems like a reasonable
(that is pessimistic and on the safe side) assumption. (applied Exploratory engineering)
This gives:
- P = TODO
- P = TODO
Note that this is (on purpose) a rather pessimistic ("conservative") estimation.
Also the assumed 1019 bearings give a total internal bearing sliding surface area of about:
S = 200m^2 -- Which intuitively feels like quite a lot but not overly excessive.
Side-notes regarding the Numbers given above
In Nanosystems 10.4.6. some examples are calculated for 1m/s sliding speed (it gives about 80MHz for the r=2nm l=2nm bearing). It's worth to note that a sliding speed of 1m/s is already quite fast. The actually proposed speeds are more on the order of about 1mm/s (1000 times slower). This makes power losses no less than one million times lower (since the two dominant drag mechanisms scales quadratically with speed).
According to Nanosystems 10.4.6.f. the two dominating effects of for friction in crystolecule bearings (at speeds of interest ) are:
- band-stiffness scallering and
- shear-reflection drag
Other drag mechanisms (acoustic radiation, band-flutter scattering, thermoelastic damping) all give negligible contributions (at least for the speeds of interest).
Numbers from papers -- less safe (since more optimistic)
For much more optimistic but less absolutely certainly on the safe side numbers there is work on coaxial carbon nanotubes: Also in contrast to crystolecule bearings nanotube bearings are already somewhat accessible to experiments.
The following is from the paper:
"Evaluating the Friction of Rotary Joints in Molecular Machines"
Assumed:
- A nanotube bearing with 0.6nm radius and 5nm length
- Bearing operating temperature: Roomtemperature 300K
- Simulation was done at the rather high speed of 30m/s ~ 8GHz
- P = 2.9(+-1.5)*10^-33 W/(rad/s)^2
Or converted into the same units as used in Nanosystems :
- P = 7.25*10^-12 W/(m/s)^2
For the above assumed 10^19 bearings this gives:
- P = TODO
TODO update chapters below
Flawless surfaces drop friction significantly
In contrast to etched micro-systems where the relative manufacturing error gets bigger with shrinking size. Atomically precise machinery has no error allow superlubrication which drops friction at least three orders of magnitude
Evolved molecular biology is not a proof that diffusion transport is the ideal solution with minimal losses
With those aforementioned effects cog-and-gear nanomachinery could potential feature smaller losses than diffusion driven natural systems (more on that comparison further down). To quantify that more in depth investigations are needed.
The issue
Nature is often (probably mostly out of psychological reasons) seen as unsurpassable. But actually it is completely unknowable whether nature as a whole will be "surpassed" by artificial technology in the far future (get side-tracked). Regardless of that, specific aspects of nature definitively can (and have been) surpassed by artificial technologies (there are countless examples).
Evolution ended up with diffusion transport and not cog-and-gear-machinery. Taken the former in to consideration that does by no means imply that this is the best or only solution. Actually evolution is facing severe limitations (lock-in-effect, incrementalism, ...).
(This is only one of the many cases where bio-analogies can have a problematic effect on perception.)
Why cog-and-gear transport may be more efficient
While diffusion transport features no friction during the transport process itself diffusion transport is not at all lossless. At intermediate passing stations some energy always needs to be converted to heat (tech term: dissipated). Otherwise the chemical reactions would not have a preferred direction to go and all the molecular "machinery" would cease to do anything.
Of course cog-and gear nanomachinery has exactly the same requirement. The big difference is that in biological systems energy often comes in discrete disconnected chunks. If ther's more than needed the excess is dissipated without being used for some desired effect. In a crude analogy it's like being unable to accept the change money.
In cog-and-gear nanomachinery everything is linked together in one big machine phase There energy can be drawn in a continuous rather than discrete fashion. The dissipation necessary for forward moving operation (arrow of time) can be balanced and minimized further down to the absolutely unconditionally required minimum. See main article: "Low speed efficiency limit"
Proposed machine speeds are WAY below speeds of thermal motion
In gemstone based nanomachinery one usually wants the operation frequencies to be well below the thermal motion frequencies. Otherwise the mechanical motions couple too strongly into thermal motions and things will get very hot very quickly. The frequencies of thermal motions can be seen in oscillation infrared spectra. Typical covalent bonds are located in the wavelength range of 3µm-30µm. This corresponds to 10THz-0.1PHz.
Related: Stroboscopic illusion in animations of diamondoid molecular machine elements
Typical operation frequencies
This is strongly depending on the method of bearing (superlubrication / single sp3 bonds as bearings / some for m of levitation / ... ) and efficiency of operations.
- For mechanosynthetic mills in a nanofactory where larger forces are present and potentially slightly inefficient mechanosynthesis is performed the low MHz range is a good target.
- For low friction bearings (like in nanomechanical computing) one can go up into the high MHz to low GHz range. This still leaves a gap of three orders of magnitude to the oszillative thermal motion DOFs.
Less soft nanomachinery => less drag
Unlike compliant bio-molecules in water stiff structures like carbon nanotubes (or bearings out of gemstone) in dry vacuum do not provide low energy low frequency rotative degrees of freedom (DOFs) to couple into. Those DOFs could (if they where present like in water) go down all the way to the microwave range: ~ 3cm & 10GHz. So overlap of mechanical motion with rotative thermal motion isn't so much of a problem even at higher operation frequencies.
Note that existing simulations of crystolecules can show a a stroboscopic effect. That can lead one to believe machine motion and thermal motion lie very close together and that consequently friction would be horrendous. This is not the case. It's just an artifact of the simulation.
Related
- Friction
- The myth that diffusion transport does not need to dissipate energy or is fundamentally more efficient.
- Superlubricity
- Levitation
- Crystolecules
- How friction diminishes at the nanoscale
- Atomically precise bearings – especially Atomically precise slide bearings
- Mesoscale friction
Nanosystems – Chapter 7 – Energy Dissipation – (page 161 to 190)
External links
- (TODO: Add ref's to relevant chapters in "Nanosystems")
- Wikipedia: Rotational spectroscopy
- Wikipedia: Rotational–vibrational spectroscopy
- Wikipedia: Infrared spectroscopy & Thermal infrared spectroscopy
References
- ↑ Eric Drexlers former homepage (webarchive): Phonon drag in sleeve bearings can be orders of magnitude smaller than viscous drag in liquids
- ↑ Viscous torque on a sphere: Landau, L, and Lifshitz, E (1987) Fluid Mechanics, 2nd ed. Pergamon Press p.91.
- ↑ 3.0 3.1 Drag mechanisms in symmetrical sleeve bearings: Drexler, K. E. (1992) Nanosystems: Molecular Machinery, Manufacturing, and Computation. Wiley/Interscience, pp.290–293.